Editor's note:
"The greater danger for most of us lies not in setting our aim too high and falling short; but in setting our aim too low and achieving our mark.” — Michelangelo
Invoking Michelangelo’s adage is a way of life for Case Farms of Winesburg, Ohio. General Manager Chuck McDaniel champions the setting of high goals by everyone in the plant; as a result, said Quality Assurance Manager Paul Storsin, “these are the words we live by.”
And they are not just words for this poultry processor, as evidenced by its quality expectations beyond industry standards, above regulatory requirements and for Gold-level audit results.
“We adhere to a philosophy that if we’re in the top 25 percent of the industry (in areas such as breast yield, Salmonella prevention), then we’re going to be a successful company,” Storsin said. “If we fall below those standards to average or below average, we’re not going to be successful.” Aiming high to Case Farms is being the best in the industry.
Storsin explained: “To be the best in the industry, you’ve got to be a leader. We’re not going to be a follower, we’re going to set the standard.
“We’re not there in all areas,” he added, “but that’s what we’re reaching for.”
CASE FARMS HISTORY. Founded in 1986 through the purchase of a processing plant in Winesburg and a hatchery in Strasburg, Ohio, Case Farms has since expanded into the Southeast with processing plants in Goldsboro, N.C., and Morganton, N.C., and a genetics division in Troutman, N.C.
This network of facilities sets the stage for one of the company’s key quality initiatives — that is, weekly meetings where each processing plant reports on its quality. “Every Monday morning we have a conference call with each of the three locations’ general managers, plant managers, quality assurance managers, sales managers and (Case Farms) president and owner, in which we discuss quality. Any problems, any complaints we may have had during the week are discussed among the three locations,” McDaniel said. “That’s pretty big incentive — not to be called to the president’s office, so to speak.”
In the meetings, a plant having a problem or customer complaint explains what happened, what was done to answer the complaint and what the plant is doing to fix the cause. Each plant assesses and records quality scores in various areas each week, and these are reviewed during the calls. Not only does this create a measurable incentive, it enables the plants to learn from one another and potentially prevent similar complaints or issues from occurring at their own plants. “If something is wrong at one location, we can learn from that,” McDaniel said. “If it’s something that can happen here, we may initiate some process based on something that happened in another location.”
Through these calls and other ongoing assessments, Case Farms President David Van Hoose and Owner Thomas R. Shelton maintain a very high level of involvement in the daily quality practices and processes of its plants, McDaniel said, adding, “I can assure you that’s probably not happening in most companies.”
PREVENTION-BASED APPROACH. The vast majority of Case Farms’ quality initiatives are based on prevention, Storsin added.
The plant has at least one quality assurance person in every department who determines whether or not to release the product from that section. For example, during packaging, the chicken’s temperature can rise up to 50 degrees, but before being shipped it has to be below 40 degrees. It is that QA person’s responsibility to check and ensure the temperature standards are met.
The plant’s chiller area provides some of its most significant preventive measures. The chicken is run through a pre-chiller to begin the cooling process, and then moves into the chiller. Then, instead of relying on a single supplier’s products, Case Farms uses antimicrobials from two separate suppliers in its chill waters. “We found that to be a nice cocktail,” McDaniel said. “It works very well.” In addition, Case Farms has plans to add a post-chill dip tank. “We have a pre-chill, we have antimicrobials in the chiller and we’re putting in a post-chill. We want to be under two percent (Salmonella count), so once again, we go overboard just to make sure.”
BEYOND THE REGULATIONS. Proactive prevention also sets the bar for Case Farms’ regulatory compliance. “With USDA, the bar is always moving, and we want to be well under it,” Storsin said. Indicative of this is the company’s continually dropping Salmonella rate. While USDA requirements are that rates be maintained below 10 percent, Case Farms maintains a consistent rate below five percent, has dropped this to 2.5 percent in recent months, and has now set its sights on consistent rates of less than two percent.
This exceeding of regulations has benefitted the plant even beyond that of quality production. “About 18 months ago,” Storsin said, “USDA forced the issue with the industry on Salmonella because the results were going in the wrong direction. But when all that was happening, we were very fortunate because it didn’t affect us — we were already there. We were well below what they were asking for.”
Case Farms’ low rate is made possible by maintaining a high quality of poultry coming into the plant. “We take it all the way back to the breeders,” said Live Operations Manager Tom David. “Our replacement breeder stock is all Salmonella free — they come to us Salmonella free.” And once in the hatchery, extra steps are taken to keep the birds Salmonella free:
- In the hatchery itself, 30 tests a week are conducted for Salmonella detection, the results of which generally run at rates of less than five percent. Swabs are taken anywhere the eggs or chicks can touch. “That’s a step we take further,” David said.
- In the pullet and breeder houses, David said, “we clean out after every flock. Sanitation is very, very important.”
- Throughout the live operations areas (as well as in the processing plant) a strict rodent control program is followed. Bait stations are set around the perimeter of all the pullet houses as well as the breeder houses, he said. “This prevents rodents from ever getting into the houses to begin with.”
- Throughout these areas, complete biosecurity clothing also is required, including disposable plastic or disinfected rubber boots, clean coveralls, hair nets and the use of hand sanitizer. “So before you enter the chicken house, you have to be suited up,” David explained. Although this is an industry norm at the breeder level, it is not as much so at the broiler growout level, though it has been increasing in recent years.
- The same standards are expected in the field at the broiler growout level. Case Farms asks broiler growers to maintain strict rodent control programs and, David added, “Most of our broiler growers clean out after every flock; that’s highly unusual.”
“All of this contributes to us getting down to two percent on Salmonella,” Storsin said. “If he’s not doing a good job in the field, we’ll see it here (in the plant).”
McDaniel agreed. “If the houses are dirty and rodents are running through the houses, more birds are going to come into the plant with Salmonella on them.”
ACROSS THE BOARD. Case Farms applies this same strategy across the board of regulations. “We are checking for Campylobacter now,” Storsin said. “We don’t have to do that. It’s something we’ve chosen to do.” In fact, he said, the plant could back off a number of its quality initiatives, and save money by doing so, while still remaining within regulatory standards. “But you’re not the best in the industry if you do that.”
Required by USDA to perform two temperature tests per day, Case Farms performs one each hour because of its importance to the end quality of the product. And where hourly checks are required, Case Farms performs quarter-hour checks. “I might be obsessive on my checks, but I’d rather be overboard on it.” Storsin said. “You can never have too many checks and too many eyes when it comes to quality and food safety.”
“From a consumer perspective, from a USDA perspective, we just feel it’s very important that we perform in those areas,” McDaniel added.
AVIAN INFLUENZA. With more and more media attention given to avian influenza (AI) questions, Case Farms realizes the importance of consumer communication and education in this area. “It is very important that consumers understand exactly what the threats are to them,” McDaniel said. “Not all avian influenzas are created equal; some are dangerous to birds but not people.”
Although the disease has not yet struck the U.S., “if it ever does happen, it could be catastrophic to the industry,” McDaniel said. If even one bird were identified as infected in Washington state or North Dakota — where chicken is not even processed — it would still affect the entire industry, he explained.
And if AI were to be detected in a bird in Ohio, all exports from the state and even neighboring states could be banned. In fact, he said, if a single flock anywhere in the U.S. were found to be infected, people would stop eating chicken. The spinach recalls of 2006 attests to that.
Because of this, not only does a plant need to take all preventive measures possible, McDaniel said, “You need to make sure the companies in your area are following a similar type of processing, because if there is avian influenza found in Ohio, by association Case Farms is guilty.”
To test for avian influenza, Case Farms draws blood from every flock and takes 15 samples from every house, testing 12 of the 15 samples. No chickens are moved forward to processing until results negating AI presence are attained. “You have to do all the preventive measures to make sure it doesn’t happen,” McDaniel said.
MEASURING SUCCESS. Case Farms undergoes a multitude of third-party audits to ensure that its quality is maintained at a consistent level. But it does not rely on these, or wait until the week of the audit to try to catch problems, said Plant Manager Paul Nelson. Rather the plant has an internal auditor whose responsibility it is to conduct monthly audits to assess operations, review all documentation and essentially do the same thing that an external auditor would do. In addition to these ongoing assessments, mock audits are conducted prior to a scheduled external audit. And in these audits, Nelson said. “We don’t mind finding things wrong.”
In all audits — both internal and third-party, each department head is responsible for his own area, must present his own documentation and answer any questions the auditors may have. This gives each area ownership of the process, Nelson explained. From the plant’s monthly internal audit, each department receives a document with results — both positive and negative.
“By the time we do the next month’s audit,” Nelson said, “they have to have answers (to any issues) back and fixed with corrective and preventive action identified. And we keep that on file.”
With a succession of gold-level achievements in its Animal Welfare, Silliker and GMP audits and attainment of the 2007 Gold Medal IPM Partner Award for pest management, Case Farms’ objective is to maintain these gold-level standings. “Once we achieve gold, we feel we have to keep it,” Storsin said. “If you can stay at that level, you know you’re doing good things throughout the year.”
While this does not mean that the plant achieves 100 percent in all areas, it has consistently maintained perfect scores in sanitation, which Storsin said accounts for its low Salmonella and E. coli counts. With each department responsible for its own audits, McDaniel credits Sanitation Manager Andy Leggett for the ongoing achievements in sanitation. “It starts with sanitation,” Storsin said. “If you have a dirty plant, you can have cross contamination.”
Case Farms also conducts audits on all its suppliers. “We don’t take it for granted that everything is like the supplier says it is,” Storsin said.
CASE FARMS FUTURE. Case Farms recently started expanding its production, jumping up from 260,000 birds per week to about 400,000 birds per week. By April, the company hopes to have that number up to 500,000, with an ultimate goal of 700,000 birds per week in the next three years.
To support the expansion, Case Farms plans to invest up to $20 million over two years — including $14 million for a new feed mill.
TEAMWORK. “Everything in this company is a team effort,” Storsin said, and a main reason he joined Case Farms three years ago was because of its people. Having worked in the industry for more than 21 years, he said, “These are some of the happiest people I’ve ever worked with. And it starts at the top.”
The company’s quality policy includes three points: a commitment to providing products and services that meet or exceed customer expectations; continuous improvement of quality and service to exceed that of the competition; and the assertion that everyone in the organization is responsible for achieving the first two objectives.
It’s all about the teamwork — knowing the people you’re working with and working well with them. “We work as a team, and not individuals, to meet and surpass our goals,” Storsin said. “With that, you can achieve any goal.”
The author is Staff Editor of QA magazine.
Plants Win 'Gold Medal' for IPM
Including Case Farms, eight companies were named as 2007 Gold Medal IPM Partner Award winners by Orkin, the IPM Institute of North America and NSF Cook & Thurber.
A pest management approach that stresses multiple methods of control, Integrated Pest Management (IPM) emphasizes minimizing pesticide use. The Gold Medal IPM Partner Awards honor companies that have shown dedication to making IPM work through vigilant sanitation, prompt adherence to structural pest management recommendations, diligent record-keeping and staff participation in IPM training.
An awards jury of IPM experts selected the winning facilities from 64 nominees throughout the United States and Canada. All the nominees employ Orkin’s Gold Medal Protection, a comprehensive IPM service that emphasizes quality assurance and documentation.
The 2007 Gold Medal IPM Partner Award winners are:
- Barry Callebaut (Saint Albans, Vt.) — cocoa, chocolate and confectionery products.
- Case Farms, Inc. (Winesburg, Ohio) — poultry processing.
- Farbest Brands (Plain City, Ohio) — custom manufacturer of liquid and dry products and distributor of specialty food ingredients.
- Morton Salt Company (South Hutchinson, Kan.) — producer of salt for grocery, water softening, ice control, agricultural and industrial uses.
- Jones Packaging (London, Ontario) — provider of packaging solutions
- Maidstone Bakeries (Brantford, Ontario) — manufacturer of bakery goods.
- Neilson Dairy (Ottawa, Ontario) — manufacturer of fresh milk and aseptic beverages.
- Parmalat Dairy & Bakery (Laverlochere, Quebec) — producer of butter and milk powders.
In its fourth year in the United States and third year in Canada, the Gold Medal IPM Partner Awards began as an effort by Orkin and the IPM Institute to encourage the use of IPM and other environmentally friendly practices.
NSF Cook & Thurber joined the awards as a co-presenter in 2007, bringing to the program its food-safety auditing expertise.
By the Numbers
At Case Farms’ Winesburg, Ohio, plant:
- The current facility, constructed in 1956, is two stories of approximately 66,000 square feet.
- There are approximately 350 employees working:
o one minimum nine-hour shift, five days per week.
o a second shift dedicated to maintenance.
o a third shift dedicated to cleaning and sanitation. - About 390,000 chickens are slaughtered per week.
Inspected by USDA, Case Farms also undergoes numerous audits, including:
- Two annual audits where the plant strives to consistently achieve a score of at least 95 percent, which is considered Gold level
- a GMP Food Safety Audit for Sysco
- a YUM audit for YUM Brand Suppliers.
- Monthly audits conducted by the HACCP coordinator and quality assurance manager in order to meet all requirements for the annual audits, as well as for GMP compliance and food safety.
- An average of 1,000 internal quality-related checks each week, with this number expected to continue to increase into the future.
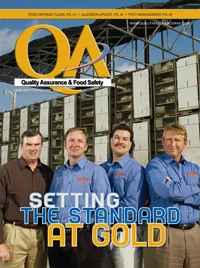
Explore the January 2008 Issue
Check out more from this issue and find your next story to read.
Latest from Quality Assurance & Food Safety
- USDA Invests Up To $1 Billion to Combat Avian Flu, Reduce Egg Prices
- Washington Cats Confirmed with HPAI as Investigation into Contaminated Pet Food Continues
- USDA Confirms Bird Flu Detected in Rats in Riverside
- Kyle Diamantas Named FDA’s Acting Deputy Commissioner for Human Foods
- QA Exclusive: Food Safety Leaders React to Jim Jones’ Departure, FDA Layoffs
- Water Mission Wraps Up Ukraine Response, Transitions to Long-Term Solution
- APM Steam Aims to Support Facility Preparedness for Winter with Steam Trap Surveys
- Therapy Helps Peanut-Allergic Kids Tolerate Tablespoons of Peanut Butter