More Than One-Fourth of Foodborne Illness Costs Attributable to Produce
Acute foodborne illnesses cost the U.S. an estimated $152 billion per year in healthcare, workplace and other economic losses, according to a report published by the Produce Safety Project (PSP). The study, "Health-Related Costs from Foodborne Illness in the United States," estimates that more than a quarter of these costs, an estimated $39 billion, are attributable to foodborne illnesses associated with fresh, canned and processed produce. The study was written by Robert Scharff, a former FDA economist and current Ohio State University assistant professor in the department of consumer sciences.
The FDA has announced that before the end of the year it will propose mandatory and enforceable safety standards for the growing, harvesting and packing of fresh produce. These will be the first nationwide safety standards for fresh fruits and vegetables.
"An up-to-date cost analysis of foodborne illnesses is critical for FDA officials and lawmakers to craft the most effective and efficient reforms," said Jim O’Hara, PSP director. "A decade ago, we spent more than $1.3 billion annually to try to reduce the burden of foodborne illness and today we are spending even more. We need to make certain we are spending limited funds wisely and hitting our target of reducing sicknesses and deaths, and this study gives us a yardstick to measure our progress."
Produce (fresh, canned and processed) accounts for roughly 19,700,000 of the reported illnesses documented, at a cost of approximately $1,960 per case and $39 billion annually in economic losses. California, Texas, New York, Florida, Illinois and Pennsylvania were the states most impacted by foodborne illness cases related to produce.
"The contribution of this study is that it provides more complete estimates of the health-related cost of foodborne illness in the United States by summing both medical costs (hospital services, physician services and drugs) and quality-of-life losses (deaths, pain, suffering and functional disability) for each of the major pathogens associated with foodborne illness," said Scharff. The costs include expenses to the person made ill as well as to others, such as insurance companies that pay medical expenses.
Scharff based his analysis on the economic principles used by FDA and USDA economists. To account for uncertainty, he utilized confidence intervals and sensitivity analysis. The cost of foodborne illness is calculated on both an aggregate level and a pathogen-specific level. The full report is available at www.producesafetyproject.org.
******
Study Finds Consumers
Alter Shopping Habits Due to Food Safety Concerns
A study conducted by Michigan State University (MSU) on behalf of the risk management company DNV is finding that U.S. consumers are highly aware of food safety issues and have high recognition of third-party certification as an effective signal of food safety assurance. Consumers strongly prefer to see products labeled as safety certified.
"Consumers are not only aware of food safety issues, they are actually changing their shopping habits due to food safety concerns," said Chris Peterson, director of the Product Center at MSU. "Nearly half of the consumers we surveyed indicated a change in shopping patterns."
These and other findings are the results of more than 400 consumers surveyed across the country representing a wide variety of demographics, education and income levels. Under the guidance of the MSU team, the surveys were conducted online by an independent research firm.
DNV Director of Food Safety Solutions Kathy Wybourn said they are now moving into the second part of the two-phase study, in which food industry professionals will be interviewed "to get their pulse on the business processes and various auditing schemes that relate to food safety."
Phase two of the food safety and safety certification research study is expected to be completed in mid April with findings available shortly thereafter.
*****
FDA Commissioner Issues an Open Letter to the Food Processing Industry
The FDA has notified 17 food manufacturers that the labeling for 22 of their food products violates the Federal Food, Drug, and Cosmetic Act. The action follows an October 2009 statement by Commissioner of Food and Drugs Margaret Hamburg, M.D., encouraging companies to review their labeling to ensure that they are in compliance with FDA regulations, and are truthful and not misleading.
As part of the prioritizing of nutrition labeling for the FDA, Dr. Hamburg wrote an open letter to industry dated March 3, 2010. The letter underscored the importance of providing nutrition information on which consumers could rely, noting, "Today, ready access to reliable information about the calorie and nutrient content of food is even more important, given the prevalence of obesity and diet-related diseases in the United States."
Hamburg also expressed her hope that the Warning Letters would clarify the FDA’s expectations for food manufacturers as they review their current labeling. The violations cited in the Warning Letters include unauthorized health claims, unauthorized nutrient content claims, and the unauthorized use of terms such as "healthy" and others that have strict, regulatory definitions.
Companies that received Warning Letters now have 15 business days to inform the FDA of the steps they will take to correct their labeling. The letters are the agency’s most recent action to help improve consumers’ ability to make nutritious choices. The FDA also plans to propose guidance regarding calorie and nutrient labeling on the front of food packages and work collaboratively with the food industry to design and implement innovative approaches to front-of-package labeling that can help consumers choose healthy diets.
See Best Practices (page 61) for more information on Warning Letters.
*****
Walmart Looks to Supply Chain to Further Reduce Greenhouse Gas Emissions
Walmart has announced a goal to eliminate 20 million metric tons of greenhouse gas (GHG) emissions from its global supply chain by the end of 2015. This represents one and a half times the company‘s estimated global carbon footprint growth over the next five years and is the equivalent of taking more than 3.8 million cars off the road for a year.
"Energy efficiency and carbon reduction are central issues in the world today," said Mike Duke, Walmart president and CEO. "We’ve been working to make a difference in these areas, both in our own footprint and our supply chain." The footprint of Walmart‘s global supply chain is many times larger than its operational footprint and represents a more impactful opportunity to reduce emissions.
Reducing carbon in the life cycle of the products often means reduced energy use, greater efficiency and lower costs for consumers, he said, adding. "As we help our suppliers reduce their energy use, costs and carbon footprint, we’ll be helping our customers do the same thing."
Walmart collaborated with the Environmental Defense Fund (EDF) to develop the approach. A team of external advisers will identify projects, quantify reductions, engage suppliers and ensure proper procedures are followed for each GHG reduction claim. The program has three main components:
Selection: Walmart will focus on the product categories with the highest embedded carbon. This is defined as the amount of life cycle GHG emissions per unit multiplied by the amount the company sells. To find the embedded carbon, the ASC reviewed the GHG emissions associated with all Walmart product categories, so as to focus on those with the greatest opportunity for reductions. Reductions can come from any part of a product’s life cycle.
Action: For a project to be included, it must reduce GHGs from a product in the sourcing of raw materials, manufacturing, transportation, customer use or end-of-life disposal.
Assessment: Suppliers and Walmart will jointly account for the reductions. ClearCarbon will perform a quality assurance review of claims to ensure methodology, completeness and calculations are correct, and PricewaterhouseCoopers will assess under consulting standards whether the defined procedures were followed consistently to quantify the reduction claim.
More information on Walmart‘s program to reduce GHG emissions is available at www.walmart.com.
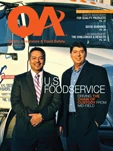
Explore the March 2010 Issue
Check out more from this issue and find your next story to read.
Latest from Quality Assurance & Food Safety
- Bird Flu: What FSQA Professionals Need to Know
- Registration Open for 129th AFDO Annual Educational Conference
- Frank Yiannas, Aquatiq Partner to Expand Global Reach of Food Safety Culture
- World Food Safety Day 2025 Theme: Science in Action
- Ancera Launches Poultry Analytics System
- USDA Terminates Two Longstanding Food Safety Advisory Committees
- Catalyst Food Leaders Announces Virtual Leadership Summit for People in Food
- Food Safety Latam Summit 2025 Set for Mexico City