Although a food processing plant has little option as to whether or not to implement a pest management program, there are numerous decisions to be made as to exactly what this program will be and who will perform the service. Should your plant contract out for the service? Should it employ internal personnel? Or should the program consist of a combination of the two?
Drawing on the experience of three industry experts, this article discusses each of the options and how a plant can make the decision. In addition, this issue’s Best Practices column discusses practical tips for making the most of your pest management program.
Our experts include:
Richard Kammerling, president of RK Pest Management Consulting and Supplies, with more than 40 years experience in design and development of pest control technologies and food safety and IPM programs.
Linda Mason, associate professor in the department of Entomology at Purdue University; co-author of the chapter “Role of the Pest Management Professional in Food-Processing Pest Management” of Insect Management for Food Storage and Processing (2nd ed., AACC International, 2006); and pest program inspector for the processing industry.
Kevin Pass, president of Action Pest in Evansville, Ind., which provides pest management services to a number of food processing facilities.
5 Reasons Plants Work with Pest Management Providers
1. EXPERTISE. The main business of a processing plant is food, so many plants do not even think about having pest management expertise — nor do they want it. Instead, if a problem arises, the plant liaison can simply call the provider and tell him or her to take care of it. In fact, according to Mason, one of the greatest advantages of using pest management professionals is their expertise. “You are bringing in someone who is focusing exclusively on that. Their full interest in your facility is looking at it from a pest management aspect,” she said.
Because pest management is the full-time job of these professionals, they are doing it on regular basis and maintaining daily expertise. When in-house personnel are utilized, it often is just one of their many jobs, and since they are not doing it on as regular a basis, it can take them longer to do the same job. And it can easily lose priority to the worker’s other duties. “Pest control always gets pushed to the bottom of the priority pile…often until something blows up,” Pass said.
2. RANGE OF EXPERIENCE. Because pest management professionals will generally work a number of different plants, they can bring a greater breadth of knowledge to your program. They will have seen a vast array of issues and lessons learned and can transfer this knowledge and customize best practices for your plant.
“Typically, an in-house person is just not exposed to the multi-dimensional aspects of pest management. An in-house person has less experience across the board,” Pass said. “I think the greatest single advantage is getting a more qualified individual,” he added, explaining that large jobs can require additional personnel. “If the company you choose has multiple employees who can be devoted to a job, you have even more of a support structure,” he said. They also have the equipment and experience to perform services that may only be needed once every few years.
3. TRAINING AND CERTIFICATION. Most pest management professionals who work in food plants have undergone training specific to this industry, and understand the specific issues plants face and the regulations under which the pest provider and plant must operate. In contrast, Mason said, “Most of the people I’ve met in-house are not trained nearly as well as pest management professionals. They have too many duties.” And, they are not as able to maintain as current or in-depth training as that most pest management companies require of their technicians. For example, they may understand how to eliminate the pests but not be as well-versed on pest attractants, and therefore have less knowledge in preventing the problem in the first place.
In addition, training and recertification seminars and programs actually can be a motivating factor for those providing service, Pass added. “We keep people interested because there’s always something new. There are more different insects than any other animal.” Typically, he said, an in-house provider does not have as much access to the training, relying instead on self-training such as books, magazines and seminars. This, along with lack of variety in the day-to-day work, can be demotivational for an in-house worker, Pass said. “They see the same place day in and day out, and they get bored with it, maybe get a little lax with walking the same beat every day.”
4. ECONOMICS AND LIABILITY. Contracting with a third party for your pest management also means that that company is responsible for all the expenses of doing so, including training, certification, equipment, products, insurance and labor. Using in-house personnel for your pest service would mean that your plant is not only financially responsible for these pieces and parts, but also must commit the time to acquiring them, storing the chemicals, providing time off for initial training and recertification. Contracting with a pest management company means you are, of course, paying that company to do so, but it is under a single budgeted service plan for pest management.
Although the plant ultimately is accountable for any food adulteration resulting from pest contamination whether the service is performed in-house or by a contractor, there are additional costs, liability and insurance needs associated with the use and storage of pesticides as well as general service performance, which is held by the pest management company. If the program is pulled in-house, Mason said, “You take on the liability if there’s a problem.”
“The risk factor is enormous,” Kammerling said. But using a good pest management company reduces that risk factor for the plant. However, he added, even when a plant is contracting out, someone at the plant needs to have at least a general understanding of the work and maintain strong communication with the supplier.
5. EYES AND EASE. Just as with third-party auditors, using the services of a third-party pest management professional provides you with another set of eyes in your plant. This provider will see things differently than the employee who is in the plant every day. For example, Mason said, an employee may no longer notice the door that is always propped open by those who smoke, or the spillage that occurs regularly — but may not be cleaned as often. A person coming in from the outside often will notice such things immediately, and this provider will see it through pest management eyes.
In addition, many plants will contract out simply because employing a licensed professional is much easier than adding this task onto an already-full plate of responsibilities. “The easiest thing is to contract it out,” Pass said. A good pest management company has existing programs that can be customized to each plant. Bringing the program in-house means supporting that program in-house — developing standards; managing the program; researching, purchasing and storing the proper equipment and chemicals; and ensuring that the assigned worker is licensed and maintains his or her certification…and doing it all over again should that person leave the company.
6 Incentives for Implementing an In-house Program
1. INTERNAL KNOWLEDGE. “The greatest advantage I see is that the employee is there and it’s not just done on a monthly basis or weekly basis,” Mason said. “If there is a problem, the person is there; if a pest is seen, that person is there.” The problem can be addressed immediately, rather than a manager making a call, then waiting for your contracted provider to become available, driving to your plant, getting briefed on the issue and, finally, addressing the problem.
While it was noted as a contractor advantage that a new set of eyes can see things employees may no longer notice, the counterpoint to this is that a provider who comes only once a month or other irregular spacing of time will only get a snapshot of your plant rather than an ongoing panorama. In addition, an internal person will know your plant and its operations, know its layout and be familiar with common issues, knowledge of which could be critical to pest prevention efforts.
2. COMMUNICATION. This ongoing availability also is advantageous for communication, Pass said. “There are really good lines of communication because their person is there all the time.”
3. RAPPORT AND CONSISTENCY. Employing in-house personnel also gives the plant control in selection and maintenance of the person performing the service. A contracted company could continually switch technicians servicing your plant, so that you are unable to develop rapport or ongoing consistency in your program.
4. SECURITY. Some areas of a food-processing plant can be very sensitive. Allowing access to such areas by non-employees can require extra security clearance as well as a comfort level with the person’s integrity. When internal personnel are used for the pest management program, security clearance generally has already been conducted. In extremely sensitive areas, Mason added, “You may even have to have an employee walk along with the vendor. So you might as well have your employee learn and do it themselves.”
5. ECONOMICS. While there are costs involved with in-house pest management personnel, there are seminars and programs for recertification available to the industry to help keep these costs in line, Kammerling said. And, in addition to the ongoing contract costs of a third-party provider are the initial costs of management’s time to research the market and sort through the sales promises to choose the best, most reliable partner for your plant.
6. AUTHORITY. Internal personnel often can be given greater authority to get a problem fixed. Say there is an issue with sanitation that is attracting pests. The third-party provider can recommend that the area be cleaned, but generally has little or no authority to make it happen. Internal personnel can attend a team meeting, explain the problem and ensure that any unresolved issues are brought to the attention of the person who can get them fixed. Often the pest management person is a part of the plant’s sanitation and/or maintenance team and can even take care of the problem himself. “Linking sanitation with pest control is one of the biggest advantages I see,” Mason said.
How Plants Integrate Both Contract Providers and In-house Personnel
When a plant chooses to employ both an in-house worker and a contract provider for its pest management, a typical division of labor is the in-house monitoring of pest traps — such as bait stations, light traps and multi-catch traps — with inspection and pesticide application run by the contractor. This split option enables the plant to use in-house personnel without having to maintain a pest control license, Pass said.
Even when a plant decides to use in-house for its pest management program, it still will likely have to contract out for big jobs, Mason said. Jobs such as fumigation require specific equipment, training and licensing that a plant will rarely have in-house. Using a contractor for the big picture responsibilities also could include their designing of the program, ensuring regulatory compliance, preparing for audits and maintaining records, while in-house personnel manage day-to-day tasks of monitoring and sanitation. In such cases, both the contractor and in-house personnel can participate in inspections and follow-up for compliance.
Additionally, the use of a contractor never absolves the plant from any pest management responsibilities. Rather, Kammerling said, a pest management program should be developed jointly between the contractor and the food processor, with the processor providing insights to the specific needs of this plant and the contractor applying the pest management expertise to that assessment. “The biggest issue that pest control contractors have when going into a food facility is that they don’t understand the job to be performed,” he explained. On the other hand, food plant personnel may be thinking, “it’s only pest control,” and not realize the importance of a thorough, well-planned program.
Whether contracting out, using in-house personnel or implementing a combination of the two, the plant needs to understand signs of pest presence, be able to recognize potential issues and include such observations in plant inspections. “Pest control is a building block to your food safety program,” Kammerling said. “Inspectors play a tremendous role in what goes on.” For example, the person monitoring pheromone traps needs to understand what constitutes a problem and realize its potential connection to storage practices. A contracted technician cannot necessarily do anything about the issue, but they can at least put out a red flag. “By working together,” he said, “you can attain what you’re looking for.”
What's Best for Your Plant?
While more plants tend to contract out for pest management services in today’s market, each of the three experts envisions a different trend for the future.
CONTRACT. In his area, Pass is seeing more companies beginning to contract out for services. A number of the plants his company services had previously used in-house personnel for pest management. He said this may be due to the increased complexity of pest management, and the increasingly narrowing list of pesticides approved for use. “You used to turn on the fogger and fog every Saturday night,” he said, but this is no longer an accepted standard.
IN-HOUSE. Kammerling has seen pest management turn in the processing industry like a revolving door. In the 1970s, most companies did their own service, but in the 1990s “the pendulum went completely around,” he said. “I think the pendulum may be swinging back again. The reason being because of the lack of competent service. If you look at the sanitation manager and quality assurance manager, many know as much or more about pest control than the pest control industry.”
BOTH. Mason sees a trend in the industry to doing more split option pest management. Utilizing plant personnel for more of the ongoing monitoring, and using contracted providers for baiting programs and pesticide application, as well as calling on the contracted provider when problems arise.
YOUR PROGRAM. Deciding which direction your plant will take means asking a number of questions, including:
- Do you have employees willing to take on the duties and have some pest control experience or are willing to train?
- Are you willing to put in the time and money for training, including initial training, trade publications, seminars and conferences necessary for recertification and staying up to date on the latest technology and techniques?
- How extensive are the pest pressures in your plant? Is your facilty complex?
- What are the regulatory requirements of your state? Do you have the internal resources for compliance?
- What pesticides would most likely be needed for control? Are you able to meet all regulatory requirements in this area?
- Are the technicians of the contract company you are considering specifically trained for food-processing operations?
- What are the standard documentation and record-keeping practices of the contracted company? Does it have an option for electronic scanning and recording?
- Will your program be in compliance with all customer-required standards?
- Would there be an advantage to a shared program in your plant, and if so, exactly how would this work?
- Is your program providing proactive prevention and corrective action rather than applying pesticides wherever possible?
The author is Staff Editor of QA magazine.
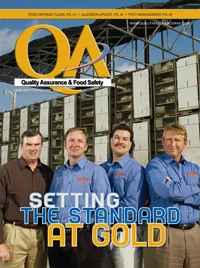
Explore the January 2008 Issue
Check out more from this issue and find your next story to read.
Latest from Quality Assurance & Food Safety
- Kim Heiman Elected to Second Term as President of Wisconsin Cheese Makers Association
- FAO Launches $150 Million Plan to Restore Ukrainian Agricultural Production
- Pet Food Company Implements Weavix Radio System for Manufacturing Communication
- Penn State Offers Short Course on Food Safety and Sanitation for Manufacturers
- USDA Announces New Presidential Appointments
- FDA to Phase Out Petroleum-Based Synthetic Dyes in Food
- IFT DC Section to Host Food Policy Event Featuring FDA, USDA Leaders
- CSQ Invites Public Comments on Improved Cannabis Safety, Quality Standards