Cost of Non-Quality
recently heard a myth/truth that it is more profitable for a food company to recall product (with an effective PR message) on an as-needed basis, as compared to all the costs associated with prevention and appraisal. What has happened to the quality management principle of measur-ing non-quality/nonconformance?
"If one can measure it (objectively), one can manage it" is a fundamental management belief. Cutbacks in quality assurance and food safety systems and/or personnel (e.g., plant/corporate sanitarians) are not a means to improve profitability. More regulatory involvement is forthcoming (see Auditor‘s Soapbox at right) with consequences of regulatory nonconformance higher than ever. What is a practical solution to this dilemma?
The first solution centers on ownership responsibility to provide sufficient resources to develop and implement sound quality assurance and food safety systems. Good ownership may be committed to providing resources, but often cannot identify what is needed or is unable to do it by themselves.
The second solution is a quality man-agement responsibility to provide justification for adequate resources necessary for sound quality assurance and food safety systems. What a quality manager really needs is sufficient information to show upper management that reducing the cost of non-quality is in fact an opportunity to increase profits.
The first step is to gather costs associated with non-quality (doing work over) such as waste, redesign, complaint handling, product replacement/destruction, rework, etc. Communicate these cost sources with solutions to improve quality and profit. Bring together a few costs such as waste and product destruction. For example, track the costs of waste removal—compactors, dumpsters and related labor, then analyze waste contents, value and cause. If the leading distribution center waste content is product contaminated with insects, resources can be made available to improve product quality by eliminating a specific waste source. Is the source open unscreened doors? Nylon screens or automatic door closures may reduce infestation and product contamination.
Reducing waste will increase profit but it is important to have an agreed-upon measurement of waste removal and analysis. The more one digs, the more one finds and the more one can improve product quality and profitability—all while justifying one’s existence.
Think of a future budget planning meeting when you say: "To give you an indication of how costly this problem is, I’ll show you the actual cost we are now incurring. To reduce this cost I need XYZ which has an ROI of less than 12 months." This approach is an efficient management technique to justify strategic resources to expand any quality assurance and food safety system.
If your company is doing things right the first time, then disregard this column. Reality is doing things wrong some of the time. Focus objective measurement and practical solutions first on the larger wrongs to improve quality and profits. Then move on to non-quality categories.
"Quality is not only free, but a bountiful source of profits." - Philip B. Crosby
*****
Food safety bills, backed by President Obama, are working their way through Congress—House of Representatives (H.R. 2749) and Senate (S. 510). The food, pet food, feed and agricultural industries will be seeing more regulatory funding, inspections, product seizures, authority expansion, etc. In the near future we will likely see a regulatory challenge to "no photographs permitted in this facility." This legal challenge might set precedence which can be used for decades to expand regulatory authority in food plants.
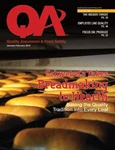
Explore the February 2010 Issue
Check out more from this issue and find your next story to read.
Latest from Quality Assurance & Food Safety
- Calbee America Launches California R&D Innovation Center
- PepsiCo Completes Acquisition of Siete Foods
- Non-GMO Project Launches Non-Ultraprocessed Foods Verification
- FDA to Hold Webinar on Updated ‘Healthy’ Claim
- High-Tech Partnership Creates Natural Blue Color for Greener Tomorrow
- Kraft Heinz Hosts Innovation Challenge for Sustainable Packaging
- FDA Requests Information on Poppy Seeds
- Danone North America Opens Applications for Annual Gut Microbiome, Yogurt and Probiotics Fellowship Grant