Imagine being involved in this scenario: A large retail customer tells you that your product is significantly (to the human eye) underweight. As you begin to investigate, you discover the problem is real and possibly has been going on for a few months. Your general manager says: “We should fire the co-packing company.” What happened? What are you going to do? Besides learning from the incident, here are three considerations.
MAKE A GAME PLAN. First, do not fire the co-packing company immediately. You will need their assistance. The co-packer should make right with you, and you should make right with all your customers. Yes, this probably means a recall. Initiating a recall will make you encounter some upset customers. But, remember, turning an upset customer into a satisfied customer makes a loyal customer. Put a game plan together and make right with all your customers.
TAKE A GOOD LOOK. Second, evaluate your co-packer. Are they cooperative? Do they have an effective and efficient quality system? Or are they uncooperative, ineffective and using their lawyers? Obtain the facts to respond intelligently to the question, “What happened, and what are you going to do?” Mandate a full report from your co-packer to get their perspective of what happened and what they are going to do to make right with your company and your customers.
BE HONEST. Third, assess your quality system. Be brutally honest! If you don’t correct a system problem now, another scenario might occur. Good systems are designed to prevent failure. Too many times a product quality system, designed from years of research, development and historical improvements, is not passed on to a production outsource. Co-packers may have one system for everything. It is expected that the GMPs, Integrated Pest Management, HACCP, SOPs and SSOPs all will be in place. This approach may work for some companies but not for others. Does your quality system or product specification have some specific requirements? They should. Differentiating your product from your competition is one example.
TAKE ANOTHER GOOD LOOK. Managing co-packers can be a scary proposition. Their use tends to be more of a business-based decision versus a quality-based one, but they do have their place. They are out of sight but seldom out of mind. Your company’s good name is on their production line; you have to trust them and their management. Their production decisions will impact your reputation and good name. Do you trust your production outsource? If not, what are you going to do? Don’t wait for a similar incident to ruin your day, week, month or even year.
EPILOGUE. What was the specific cause of this scenario? The investigation identified a 4:00 a.m. maintenance call to repair an inoperative trickle feeder on packing line “D.” This line is used exclusively for co-packing and does not contain check weighing equipment. The work order indicated an imbalance problem on a side scale used to verify weight values. The side scale counter weight was lightened slightly. Nothing was done to the trickle feeder itself. Since the repair activity, records indicated unusual inconsistency in the package weight but above declared value. The maintenance employee was not available, as he resigned the next day. There was no supervisor sign-off on the work order.
The author has spent more than 30 years in food quality assurance. He is a Certified Professional Instructor and can be reached through www.qualitycenteredconsulting.com or by calling 816/436-1627.
Auditor's Soapbox
2007 was not a good year for food safety. The reputation of food in the United States of being the safest anywhere in the world is being challenged. The globalization of ingredients, import deliveries, border surveillance, production outsourcing, building deterioration and employee downsizing, along with regulatory agency staff shortages, is creating a higher-risk food supply. Quality systems are being challenged with a need to take on broader responsibility. Is it possible that ingredient suppliers or co-packing operations are not being evaluated and approved by Quality Assurance departments or their designates? If ingredient suppliers and co-packers do not understand requirements, how could they possibly meet expectations?
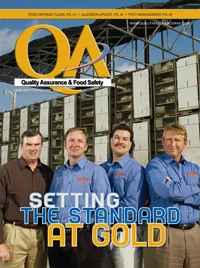
Explore the January 2008 Issue
Check out more from this issue and find your next story to read.
Latest from Quality Assurance & Food Safety
- Calbee America Launches California R&D Innovation Center
- PepsiCo Completes Acquisition of Siete Foods
- Non-GMO Project Launches Non-Ultraprocessed Foods Verification
- FDA to Hold Webinar on Updated ‘Healthy’ Claim
- High-Tech Partnership Creates Natural Blue Color for Greener Tomorrow
- Kraft Heinz Hosts Innovation Challenge for Sustainable Packaging
- FDA Requests Information on Poppy Seeds
- Danone North America Opens Applications for Annual Gut Microbiome, Yogurt and Probiotics Fellowship Grant