Total Quality Management; Lean Manufacturing; CARVER+Shock; Six Sigma®; ISO 9000 – simply more quality buzzwords, assessment lingo, process catchphrases? Perhaps. But the management tools and systems have their place in plant processes and should be understood for potential implementation – whether in their entirety or as selective tactics and practices integrated within your existing system.
For this article, which will provide a basic overview of seven general and proprietary management processes, the tools and systems will be roughly divided into three categories – with acknowledged overlap between the three. Included are:
• Risk Management
• Examples: CARVER+Shock; Triangle Risk Assessment
• Purpose: to assess vulnerabilities in relation to food defense for creation of a pertinent defense plan
• Total Quality Management (TQM)
• Examples: Six Sigma; ISO 9000
• Purpose: to manage and measure consistency of process in order to deliver a quality product
• Process Management Tools
• Examples: Lean Manufacturing; Control Factor Analysis; Statistical Process Control
• Purpose: each tool is designed to address and control a specific process factor or problem (e.g., waste, out-of-control parameter, variation)
RISK MANAGEMENT
CARVER+Shock is the assessment tool used by federal agencies for food defense against intentional contamination or attack. It is a part the Strategic Partnership Program Agroterrorism (SPPA) Initiative – a joint effort of the Department of Homeland Security, USDA, FDA and FBI in collaboration with private industry and the states to help secure the nation’s food supply. The risk assessment tool, as adapted to the food industry, is used to perform vulnerability assessments to identify the points in the plant and its processes which are most vulnerable to intentional contamination. The intent is that the plant would then focus its resources on protecting these points.
The name also has been adapted, using the basic CARVER acronym for key factors affecting the desirability of a target, and adding a seventh attribute:
Criticality – public health or economic impact
Accessibility – physical access to target
Recuperability – ability of the system to recover from the attack
Vulnerability – ease of accomplishing the attack
Effect – amount of actual direct loss from an attack
Recognizability – ease of identifying target
+Shock – the literal shock value; that is the combined health, economic, and psychological impacts of an attack.
The CARVER+Shock assessment assigns a ranking for the attractiveness of a target based on a scale of one (least attractive/lowest vulnerability) to 10 (greatest attraction/highest vulnerability), with specific scales having been defined by FDA and USDA for each of the seven attributes. By assessing the various areas and elements in a food plant with this scale, managers can identify most likely areas of attack and apply resources to these points.
As with most assessment/management systems, the plant sets up a team to conduct assessments, based on plant-established parameters such as the supply chain to be assessed and the potential threat, attacker and agent of attack. The first step in analysis is detailing that which is to be assessed, e.g., creating a flow chart of an ingredient supply chain, down to the smallest subsystem, or "node."
At this point, each node is ranked (as defined above) for each of the seven attributes. Those with the highest scores have the highest potential for attack and should have plans developed to minimize their attractiveness. Plans could include increased security at the target site, limiting of personnel access, etc.
Triangle Risk Assessment. A tool developed by TRAP-IT Security Inc. (an acronym for Triangle Risk Assessment Process) was detailed during a session of the 2005 Worldwide Food Expo by President Bob Havrilak. The process, best described by the company’s logo triangle – an R (for risk) encompassed by three labeled sides: Threat, Target and Access. The company’s process is a step-by-step computerized system with which food professionals can evaluate the vulnerability of their facilities, and security professionals can develop defensive strategies to mitigate the potential for terrorist attack.
With the triangle’s sides further defined for defense of the food industry as: Threats being people, Target being food, and Access being proximity, the goal of the process is to break the triangle to eliminate risk. That is, by:
• managing the threats – including company personnel as well as any persons in or near the plant, such as vendors, suppliers, customers, etc. For example, create a hierarchy protocol for facility entry wherein each person is assigned specific entry rights with specified procedures associated with this clearance.
• hardening the targets – through two key food security strategies...
à perimeter security including locks, ID screening, security guards and policies as countermeasures to enforce security clearances.
à target-based security focusing on securing individual food targets; allowing only authorized people to work in direct contact with raw materials, work in process, product and packaging; and including countermeasures such as tamper-evident containers, seals, guards and access policies.
...you prevent Threats from Accessing Targets, thereby containing risk.
Like CARVER+Shock, the process begins with the identification of a Facility Security Team. The objectives are then to:
• identify vulnerable points in the facility
• characterize the threats
• strengthen any weaknesses
• eliminate threats
• create an early detection system
• develop a response plan.
Having a response plan in place and training on the plan is critical for immediate, organized and consistent response to a security breach. The security plan should also go a step beyond the plant to enable traceability from field to fork, with FDA requirements for one forward/one back inventory records integrated into the plan.
Havrilak developed the triangle process because it is easy to understand and teach, and it provides an effective method of analysis as well as a structure for solution. Most important to creating a defense plan, though, he said is getting organized and choosing a planning process. "They [FDA] don’t care what method you use as long as you do something." The process does, however, need to be creditable, documentable and auditable.
TOTAL QUALITY MANAGEMENT
Six Sigma is a process-improvement, problem-solving technique designed to improve business performance, said Don Redinius, principal, Advanced Integrated Technologies Group Inc. in a session of the 2005 World Wide Food Expo. Redinius has had experience with a number of process-improvement systems, but, he said, "this was something I could get excited about!"
Though Six Sigma is a quality management technique, "it is not just about quality," Redinius said. "It is a business and process management system, and one of the many outputs is improved quality." Applied as a management tool for achieving a company’s vision, key goals and objectives, it focuses on variations and measuring and managing these within specific parameters in order to produce consistent quality. "Six Sigma will change the way you think, the way you view work and the way you get work done."
The system is implemented as an enterprise-wide strategy to determine problem areas, define improvement initiatives and derive and implement solutions "in a predictable and repeatable manner to improve business results." It incorporates four premises toward this end:
• methodology tools and tactics – focusing on cause and effect through "DMAIC" – define, measure, analyze, improve, control – implementing analytical problem-solving tools and management structure to achieve results
• business strategy – implementing employee development and capability to achieve a profitability improvement goal of 40 percent or more
• philosophy of operational excellence – setting a goal for process outcomes with less than 3.4 defects per million
• process measurement and management – measuring, monitoring and managing significant outputs through a set process
Because, Redinius explained, "most of the time it’s variation the causes our problems," the system involves a strategy to:
1. recognize the areas which need improvement to meet business goals
2. define projects, determine what needs to be resolved to eliminate problematic areas
3. understand the relationships between associated processes
4. improve performance by reducing variation and centering processes of key outputs and establishing long-term sustainable process performance and control.
Rather than general teams, this system has designated titles and responsibilities, with project mentors, or "black belts," undergoing extensive training and generally committed full time to the position. "In many cases, Master Black Belt is a career," Redinius said. While company executives set the vision and expectations, the system is run by "champions," who set the plan and select participants and projects, and the "belts," including black who mentor projects and train participants, and green and yellow who work on teams to define solutions, and implement and sustain process improvements.
While Six Sigma generally starts out as a quality management system for a company, Redinius said, it evolves to become a business and process management system, and eventually becomes a core competency for employees, with employees able to quickly and accurately solve problems, align and optimize business processes and make better decisions.
ISO 9000 is a set of standardized requirements for a quality management system. Developed by the International Organization of Standards (ISO) in Geneva, Switzerland, it is governed in the U.S. by the American National Standards Institute (ANSI) and the American Society for Quality (ASQ).
Implemented by organizations in more than 150 countries, ISO 9000, according to a brief by ISO, "has become an international reference for quality management requirements in business-to-business dealings." It is actually a "family" of standards, with specific topics including:
• ISO 10006: project management
• ISO 10007: configuration management
• ISO 10012: measurement systems
• ISO 10013: quality documentation
• ISO/TR 10014: managing the economics of quality
• ISO 10015: training
• ISO/TS 16949: automotive suppliers
• ISO 19011: auditing
Originally containing 20 specific elements, the ISO 9000 standard was revised in 2000 (ISO 9001:2000) to be more generic, enabling application to any business or administration in any industry or government sector that provides a product or service. In the context of ISO 9000 standards, the brief continues, "the standardized definition of quality refers to all those features of a product (service) which are required by the customer." Quality management, then, is what the organization does to ensure customer quality requirements and satisfaction, while complying with applicable regulatory requirements and achieving continual performance improvement.
The standard, however, is based on the way an organization does its work, not the results, with the understanding that process management directly affects outcome. The steps to implement ISO 9001:2000 are:
1. Identify your goals – such as efficiency, profitability, customer satisfaction, market share increase, improved communication, etc.
2. Identify others’ expectations – including those of customers/consumers, employees, suppliers, shareholders, society
3. Obtain information about ISO 9000 (www.iso.org)
4. Apply the standards – for internal improvements, certification, or toward application for a national quality award
5. Obtain guidance on specific topics (above)
6. Assess your current system to determine gaps in ISO compliance
7. Determine processes applicable to supplying your customer
8. Develop and implement a plan to "close the gaps" in step 6 and develop processes in step 7
9. Undergo periodic assessment (and auditing if required)
10. Continue to improve the business
Certification of a company’s adherence to ISO standards is provided through documentation of an audit by an authorized third party, verifying that the company conforms to the requirements of the standard. Registration is the recording of the certification. However, ISO 9001:2000 can be implemented without having it certified or registered. Because the standards are voluntary, an organization can implement them solely for improved effectiveness and efficiencies – without the cost of a certification program.
PROCESS MANAGEMENT
Lean Manufacturing, sometimes simply termed "common sense manufacturing," is about eliminating waste, simplifying systems, improving the flow-through process, and producing according to customer "pull" – in essence doing as much as possible with as little as possible. Lean manufacturing is not new, rather its origins are variously attributed to Benjamin Franklin (in his writings, Poor Richard’s Almanack and The Way to Wealth), Eli Whitney (his perfection of interchangeable parts), Henry Ford (inexpensive mass production) and Toyota (Just In Time Production). In the Toyota Production System, Lean is defined by three Japanese concepts: kaizen - constant process analysis, kanban - "pull" production, and poka yoke - error-proofing.
Embracing the philosophy that the elimination of waste improves quality and reduces costs and production time, Lean focuses on the reduction of seven wastes:
• over-production – producing more product than is needed before it is needed
• waiting – time delays, downtime, idle time
• transportation – material in transit, therefore providing no product value
• processing – nonessential steps or procedures which do not enhance the product for the customer
• inventory – materials in storage (unprocessed or awaiting distribution), which are costly and run the risk of damage
• motion – unnecessary action of people or equipment
• waste – defective units impeding flow-through and wasting handling time and effort
The Lean process is driven by five areas: cost, quality, delivery, safety, morale. It differs from other processes in that it is a way of thinking, focusing on value-added flow and the efficiency of the overall system, rather than a set of techniques or steps for improvement. For example, Lean emphasizes the assessment of a product and its assigned costs at the point of design. It is at this point that most costs are assigned, but an engineer may seek and reduce his risk by specifying familiar materials rather than potentially less expensive, more efficient ones. Lean companies adopt a thinking, which is extended to all employees, who are trained and empowered to work toward minimization and process improvement.
As explained in Wikipedia, "Lean is basically all about getting the right things, to the right place, at the right time, in the right quantity while minimizing waste and being flexible and open to change."
Control Factor Analysis is a method to improve plant efficiencies through an applied process to determine the source of a specific problem affecting production efficiency and correct it. Presenting at the 2005 World Wide Food Expo, Trevor Cusworth, CEO, and Paul Pickersgill, Vice President and Senior Consultant, Hagen & Co. (Marblehead, Mass.), used a sauce drier example to describe the method’s six-step process:
1. Definition – what is the problem; what is the out-of-control parameter and how is it supposed to behave; and what is seen upon examination of an individual failure and a series of failures. Example: there is a variation in the moisture content of dried sauce. The sauce should be a constant 4 percent at drier discharge, but is varying from 2 to 8 percent.
2. Control Factor List – determine what the process factors are which could be causing the problem. What is the moisture content mass and timing of the sauce going in, what factors are affecting moisture removal.
3. Control Factor Behavior – check each of the process factor’s actual behavior against supposed/required behavior. Any which do not comply become a potentially contributing factor for analysis. Conduct an analysis to determine failure points within the factor.
4. Explanation and proof – In writing, detail the cause and effect to explain how the actual behavior caused the failure. If the statement explains the observation of step 1, move to step 5, otherwise continue analyses.
5. Action – Determine how to bring the parameter permanently under control, and test.
6. Improvement – Educate personnel on revised procedures and train on effective root-cause problem-solving techniques.
Statistical Process Control (SPC) uses statistical tools to identify and control the root cause of process variation. Because HACCP systems take an attribute approach to analyzing data, the integration of an SPC system can increase the efficacy of a HACCP plan. "Process control measures how stable your process is and how able it is to meet specifications," says Jeff Cawley, vice president, Northwest Analytical, in Portland, OR. Thus application of the manufacturing analytics can strengthen a HACCP program. At the core of the process, he explains, are two questions:
1. Is the process stable; is its behavior dependable and reproducible?
2. What is its capability to meet specifications?
A process capability report compares a histogram with the +/- 3 sigma process capability of the data to the tolerance (upper specification – lower specification). "The ideal is that your process capability fits way inside your tolerance," Cawley says. "So even if your process shifts, you won’t be producing bad stuff."
Managing your process with SPC is one thing that enables you to have a successful HACCP program, Cawley adds. "By having stable and very high capability processes, you give yourself very high safety margins."
Northwest Analytical’s software integrates with any of the quality systems, with the analytics of the software impinging on several places, for effective management and improvement of plant processes and supply chain performance. While you could chart a few processes by hand or on a spreadsheet, such methods limit your ability to actively manage and improve them. "You really want to manage all the processes in your plant by exception," Cawley says, explaining, that if he were monitoring 20 parameters, "software can crank through the data and alert me if one is drifting, much more efficiently." Even more importantly, the analysis provides data by which to set and take responsive action. "The value-add to SPC is not that you can create a nice control chart, but that you can read it and respond to it," he says. "In modern production that is essentially impossible by hand."
But whether the topic is TQM, Six Sigma or another such method, he says, "basically these are disciplines which allow you to organize the methods and tools people use to measure and improve a process." The differences are how you approach examining your processes – Six Sigma emphasizes designed experiments to identify areas for improvement; Lean emphasizes minimization, utilizing as clean and simple an operation as possible; ISO 9000 is a way of codifying quality or supply chain management with agreed-upon standards.
But integral to all of them are integration of your complete process and continued improvement. If you view your process areas or departments as separate entities, it really holds you back. "You’ve got to see it as an integrated system," Cawley says. And you can’t simply conduct a quality project then say, as was often the old thinking, "We’ve got it in control, now we can go back to making stuff," he says. You have to integrate continuous improvement into the system. "You need to hold your gain. Entropy is always there. If you’re not on it all the time, you will lose your gain." QA
Get curated news on YOUR industry.
Enter your email to receive our newsletters.
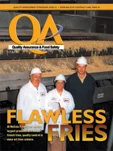
Explore the October 2006 Issue
Check out more from this issue and find your next story to read.
Latest from Quality Assurance & Food Safety
- Q&A: Sandra Eskin Leads Food Safety Advocacy Organization, STOP, as CEO
- STOP CEO Eskin on Government Layoffs, Challenges in Food Safety
- Mission Barns Announces Cell-Cultivated Pork Fat Launch Following FDA Clearance
- Hearthside Food Solutions Recalls Breakfast Sandwiches Due to Undeclared Allergen
- Walker’s Wine Juice Recalls Pumpkin Juice Due to Botulism Risk
- The Cascading Food Safety Impacts of Tariffs on the Food Industry
- Tyson Ventures Calls Startups to Apply for Tyson Demo Day
- Student Finalists Selected for IFT Product Development Competitions