Whether you’ve worked with a contract laboratory for years or you are just beginning with a new lab or implementing new tests, chances are there are ways that you can increase the efficiency and effectiveness of your sample testing. To get the most out of your relationship, the contract laboratory industry has five key recommendations:
1. Know what you need; and get what you want. The best thing that plants can do when providing samples to a contract lab for testing, says David Goins, president of Q Laboratories, Inc., Cincinnati, Ohio, is to "provide us with as much information as possible as to what they are trying to accomplish with the sample." Without complete information, Goins says, effort and money are likely to be wasted in the testing of areas which are not needed. Is it a routine analysis, or was the sample drawn because of a customer complaint or a surveillance inspection? Do you need quantitative results or a simple yes/no? You also will want to discuss areas such as required turn-around time and pricing if you’ve not worked with this lab in the past.
Goins recommends that plants discuss the testing with the lab prior to sending the test sample, particularly if it is in relation to a new program, such as a new HACCP integration or environmental testing. In many cases when feasible, he adds, Q Laboratories will go out to the facility and do a walk through to determine the best testing, methodology and analysis for the program.
While there are certain required tests, the contract laboratories want you to know that you have options. Methodologies can be customized to the needs of each specific food plant as well as each specific sample. Many plants assume that the way the lab runs testing on a regular basis is the only way that it can be done. But that’s not true, says Brett Goodrich, lab manager for Northeast Lab Services, Waterville, Maine. "We’re here to provide whatever service they need. Don’t be afraid to ask if we can provide an out-of-the-ordinary service."
2. Attaining the sample. Whether the sample being sent for testing is your actual product or an environmental swab, care needs to be taken to ensure the sample remains sterile and viable. One of the greatest challenges that contract laboratories face is attaining sterile samples from the packages sent to the lab, Goodrich says. This is primarily because of the diverse ways in which samples are sent. Thus, it is a good idea to talk with your contract laboratory to determine the best meth-od for gathering of samples; this may be utilizing packaging provided by the lab or it may be the sending of a completely packaged product from which the lab can draw a sample. Again, the labs are generally quite versatile in working with plants, but in all cases, Goodrich says, "you should minimize handling of the samples and have no handling at all by hand."
Once you have your sample, you will need to be sure it is completely labeled. Sometimes this can be done directly on the packaging, but more often, you will need to fill out the laboratory’s standard sample submission form, than use a reference number or code on the sample packaging to associate the sample with the form. By using a separate sheet, Goins says, you are able to provide more detailed information in a readable form than you generally could on the sample’s packaging.
3. Shipping the sample. Contract laboratories will generally provide instructions for shipping of a particular sample, and will often provide the supplies to do so. It is important that all instructions for packaging, labeling and shipping be carefully followed, and if you have not received instruction, you should take the initiative to ask. According to Contract Laboratory, Inc., which provides web-based resources for laboratory outsourcing and procurement services, consideration should be made for:
a. time limits – analysis may require a specific timeframe for testing in relationship to the date/time the sample was colleted.
b. temperature – know if the sample requires specific temperature maintenance, and have a method to enable this (e.g., a shipping cooler) both before and during shipping, and ensure the external shipping package is labeled with this information.
c. labeling – in addition to temperature labeling, know and follow labeling requirements for all samples; check with your lab contact if you are unsure.
d. international – if a sample needs to be sent outside the U.S., you may need to work with a specialized customs broker to ensure all specifications are met.
e. communication – always notify your contact at the contract laboratory when you have shipped a sample and provide him or her with the tracking information.
4. Understanding and using the results. Lab analyses and reports can be complicated documents, and when received during a hectic plant run, it can be all too easy to glance at the document to ensure nothing is out of spec, then drop it in a file and continue on with business. Instead the results should be used to help you improve your business – and if the analysis appears too complex or you have any questions on it, Goins says, "we encourage them to call us for interpretation of the results" as well as how to take the results and use them to improve their systems.
An example Goins gave of testing for improvement is the use of long-term shelf-life studies, in which samples are pulled over time. Rather than simply taking each result and filing it if it is within specifications, the plant can use the shelf-life data to go beyond the basic data and answer questions as to what the results really mean to the company and its products. Can shelf-life be extended for the product? Would this be a good thing to do? In addition, full review of interim reporting can save a company time and money – if the product is failing early, the testing can be cut off and re-implemented after the problem is fixed.
5. Maintaining a system. Whenever possible, you should have a single point of contact on each side of the testing relationship. That is, appoint one person in your plant to be responsible for handling of test samples and ask to be assigned a specific contact at the lab. If you work with more than one laboratory, you can still maintain a single representative at your plant, and, again, request the single contact at each lab with which you work.
The point-to-point contact will simplify your system and enable quick and complete communication in case of situations such as contract changes, emergencies, result discrepancies, etc. In addition, if your plant does use multiple contract labs or has many different products tested or tests performed, Contract Laboratory, Inc. recommends the use of laboratory databases, spreadsheets or software to manage and track the status and turn-around time of samples and testing.
While testing standards can be strict and areas such as sterility and shipping often require the following of stringent protections, your contract laboratory program and relationship can be as individual as your plant. In fact, the more questions you ask to enable customizing of your testing, the more effective and applicable your program will be. QA
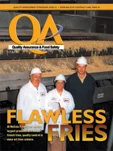
Explore the October 2006 Issue
Check out more from this issue and find your next story to read.
Latest from Quality Assurance & Food Safety
- Ferrero Group Invests $445 Million in Ontario Production Facility
- Nelson-Jameson Announces Grand Opening for Pennsylvania Distribution Center
- Taylor Farms Linked to Romaine E. coli Outbreak as Marler Clark Files Multiple Lawsuits Against Supplier
- IAFNS Announces Winners of Emerging Leader Awards for Food Safety, Nutrition
- FDA Shares Testing Results for PFAS in Bottled Water
- Provision Analytics Adds Food Safety Expert Jennifer Williams to Strategic Advisory Group
- Boston Sword & Tuna Protects Seafood Safety with Mettler-Toledo Metal Detectors
- IFT Releases New Resources to Aid Food and Beverage Industry in Sugar Reduction