Implementing a Quality Management System (QMS) is more than selecting a standard and handing it over to the quality assurance team. It is the creation of a culture, a focus on trends and the use of results to build a better business.
Create a culture.
“If you want to make the standards work, they have to become the fiber of the business,” said Carmine Liuzzi, vice president of SAI Global. “You should literally be running your business using the standards as the foundation for building and operating your business.”
As such, a QMS should have documented, measurable objectives. All employees should understand the objectives and know their role in supporting and achieving them. And, Liuzzi said, “The objectives need to be challenging so they make the organization do something differently—and better—than it is currently doing.”
“This isn’t an event, this is a new way of going forward,” said Brent Wallen, Qualtrax food safety product specialist, explaining that the system and its objectives need to be pushed to the lowest level of the organization. This is not to say that employees should be spoon fed, rather that everyone should be held accountable for quality.
“When you have your third party auditor come in, do you get nervous?” Liuzzi asked. “If yes, that is your warning that you don’t have the system into the fiber of your company. When that auditor walks in the door, it should be a non-event.”
In addition to measurable standards and recordkeeping, a successful, ongoing QMS also requires regular review. “You have to be able to use the inputs and outputs from your quality records to identify areas of improvement,” Wallen said.
Such records should track key performance indicators, which were identified based on risk assessment, then tracked for trends—both positive and negative.
The system should then become the means of managing food quality, safety and risk, Liuzzi said. “It’s not simply combining like requirements for quality, environmental health and safety, it is actually taking the time to understand and integrate them into everyday operations.” To truly provide value to the business, he said, the system also needs to go beyond merely meeting minimum standards.
Focus on Trends.
While the reviews should involve meetings of the QMS team, such meetings need to be well coordinated for productivity and focus on the process and progress of key performance indicators rather than on single events.
“This will allow us to start identifying trends as opposed to dealing with some short-term fluctuations,” Wallen said.
“I’m anti-event driven,” he added. “We’ll occasionally stub our toe, but let’s keep moving down the path. Don’t let a single event dominate a meeting if it’s not a trend.”
Because plant products, processes and size vary, the recommended frequency of meetings varies as well. But there is commonality, he said, “You need to meet often enough that you have meaningful dialogue, but far enough apart to spot trends.”
Once a trend is identified, the next step is to drill down to the root cause, Wallen said. Then corrective action can be determined, and a long-term solution developed and implemented.
To determine if your organization is incorporating a long-term focus, ask the question, Liuzzi said, “Do we put Band-Aids on things or do we actually have a root cause analysis to prevent recurrence of that type of problem?”
Meeting results will then help you identify gaps, Wallen agreed. “Ideally, you’re looking for the gaps in your strategy and looking for a long-term solution.”
Build a better business.
While focusing on trends, participants should not lose sight of the standards, but address them in a larger context. Understand what the standard is looking for; know what the plant is doing to comply. Then, Liuzzi said, ask yourself: Are we doing it like we say we are? How do we know this way is best? How do we know our system is operating properly? What are our metrics? Are they set simply to meet standards or will they improve our business?
A good QMS provides a baseline against which a company can “look honestly in the mirror and ask, ‘How are we doing?’” Many organizations don’t take the time to see how they are actually doing, or don’t like what they see in the mirror, Liuzzi said. “It can be a sobering exercise but a necessary one. Once we recognize that there is an opportunity, the organization has to have the stomach to take the medicine to get back on the right track.”
If the QMS is fully implemented, is integrated into company culture and is tracking trends—not events, it will bring value through better business practices and truly becoming part of the fiber of the business.
At that point, the QMS simply becomes the way of doing business, so that a processor can say, Liuzzi said, “This is how we conduct our business every day because it is just the right thing to do.”
The author is Managing Editor of QA magazine. She can be reached at llupo@giemedia.com.
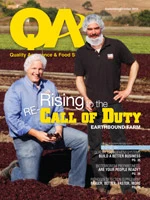
Explore the October 2010 Issue
Check out more from this issue and find your next story to read.
Latest from Quality Assurance & Food Safety
- Taylor Farms Linked to Romaine E. coli Outbreak as Marler Clark Files Multiple Lawsuits Against Supplier
- IAFNS Announces Winners of Emerging Leader Awards for Food Safety, Nutrition
- FDA Shares Testing Results for PFAS in Bottled Water
- Provision Analytics Adds Food Safety Expert Jennifer Williams to Strategic Advisory Group
- Boston Sword & Tuna Protects Seafood Safety with Mettler-Toledo Metal Detectors
- IFT Releases New Resources to Aid Food and Beverage Industry in Sugar Reduction
- Yum! Brands CEO David Gibbs to Retire in 2026
- Penn State Extension Offers Short Course on Food Microbiology and Safety for Food Plant Workers