Is everyone on the same page here?
Communication and transparency are cornerstones of an effective cockroach control program and Integrated Pest Management (IPM) overall. Another key: setting expectations. Which audits does your facility undergo, and what pest management requirements must be recorded? What’s the pest pressure history?
Based on our State of the Cockroach Control Market research, 63% of respondents depend on their pest control company alone to keep out cockroaches and other unwanted guests. Another 29% enlist in pest management services to coordinate with internal staff dedicated to these duties.
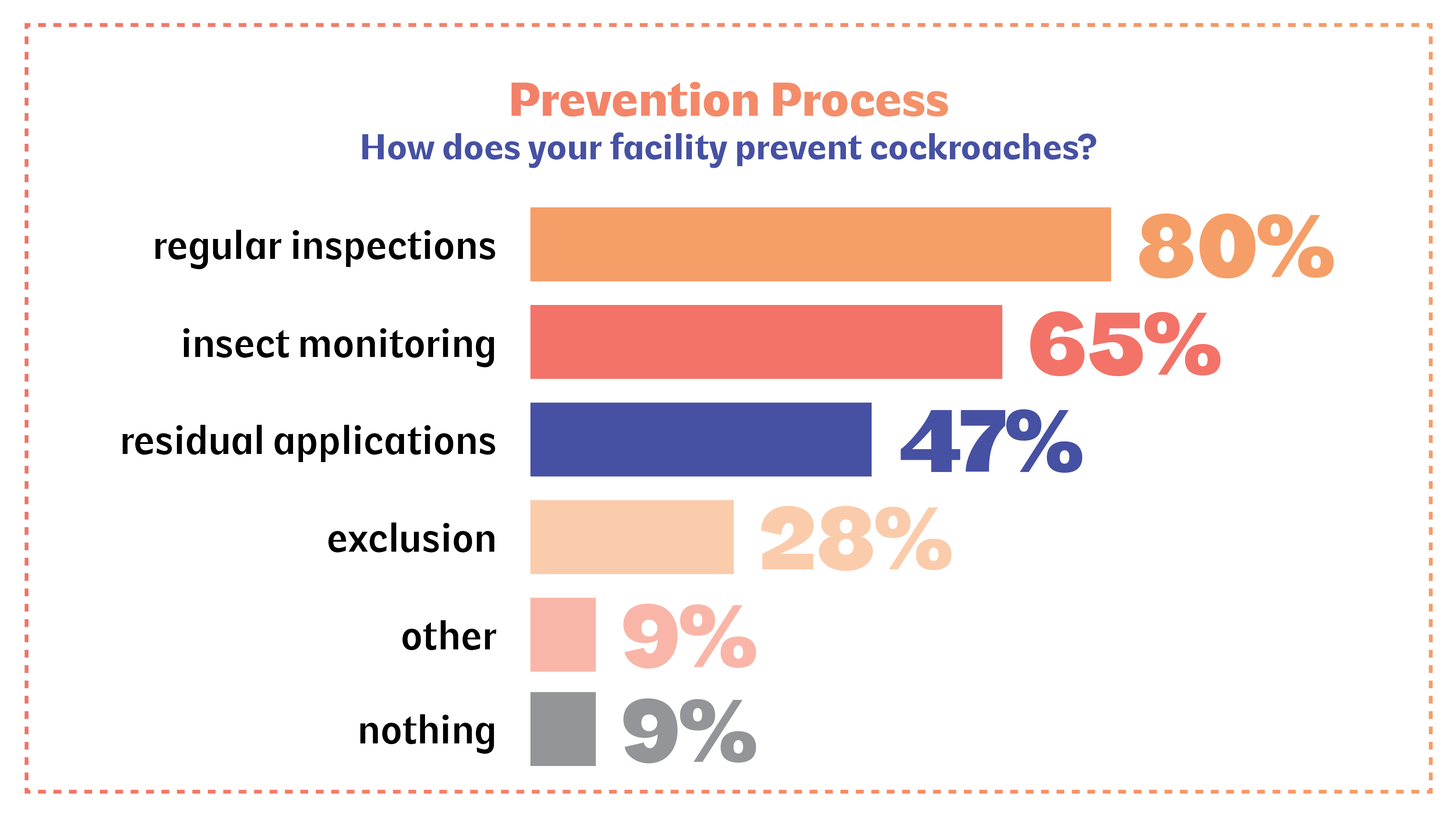
Here are some important strategies for a collaborative, successful pest management effort.
FIRST, ASSESS. “A thorough risk assessment is needed in establishing the control program,” said Patricia Hottel, technical director, Rentokil-Terminix. “It’s the foundation of the program, and depending on the facility, this effort could take several days.”
Be prepared to pay for the assessment, Hottel added.
Also important: Discuss audit standards to ensure the pest provider understands specific requirements, which can change. “It’s a good idea to make sure that information is on the contract,” said Chelle Hartzer, B.C.E., PCQI, 360 Pest Consulting. “Most are fairly similar, but there are tweaks here and there in audit standards. This should be discussed up front with the initial contract.”
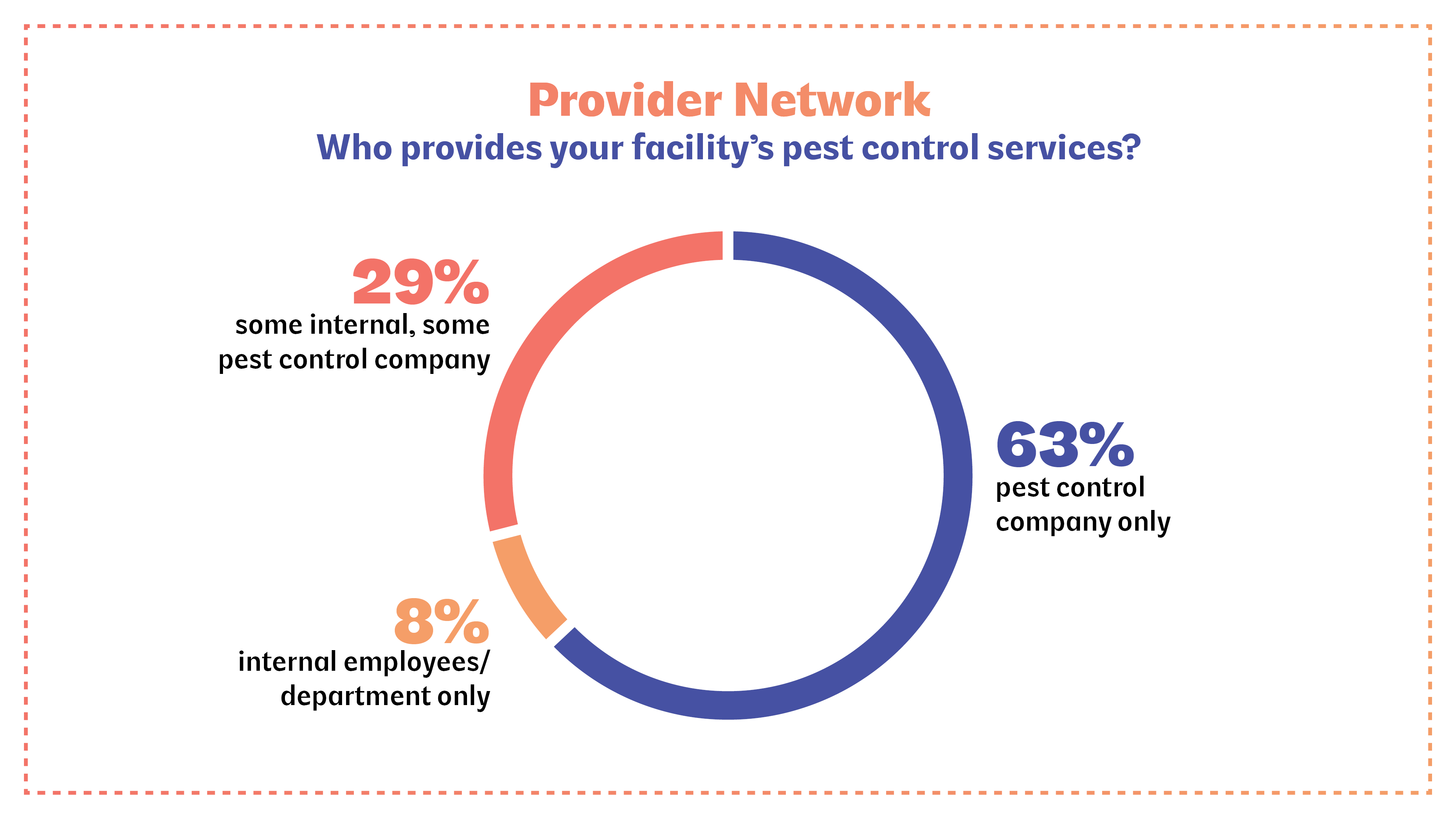
Share audit results — the good news and needs- improvement checklist.
“When possible, it can be helpful to have the pest management professional on site for the pest portion of an audit,” Hottel said. “Also, be sure to notify the PMP if there is a change in auditing companies since there may be some differences in auditing requirements.”
Following a thorough assessment, review findings and loop in all in-house stakeholders. “There will be certain program elements that must be completed either in partnership with the pest management professional or by the processor,” Hottel said. “Discuss the scheduling of each response and action item.”
SPEAK UP. “It’s better to be overly communicative,” said Sydney Crawley, principal vector scientist, Rentokil-Terminix.
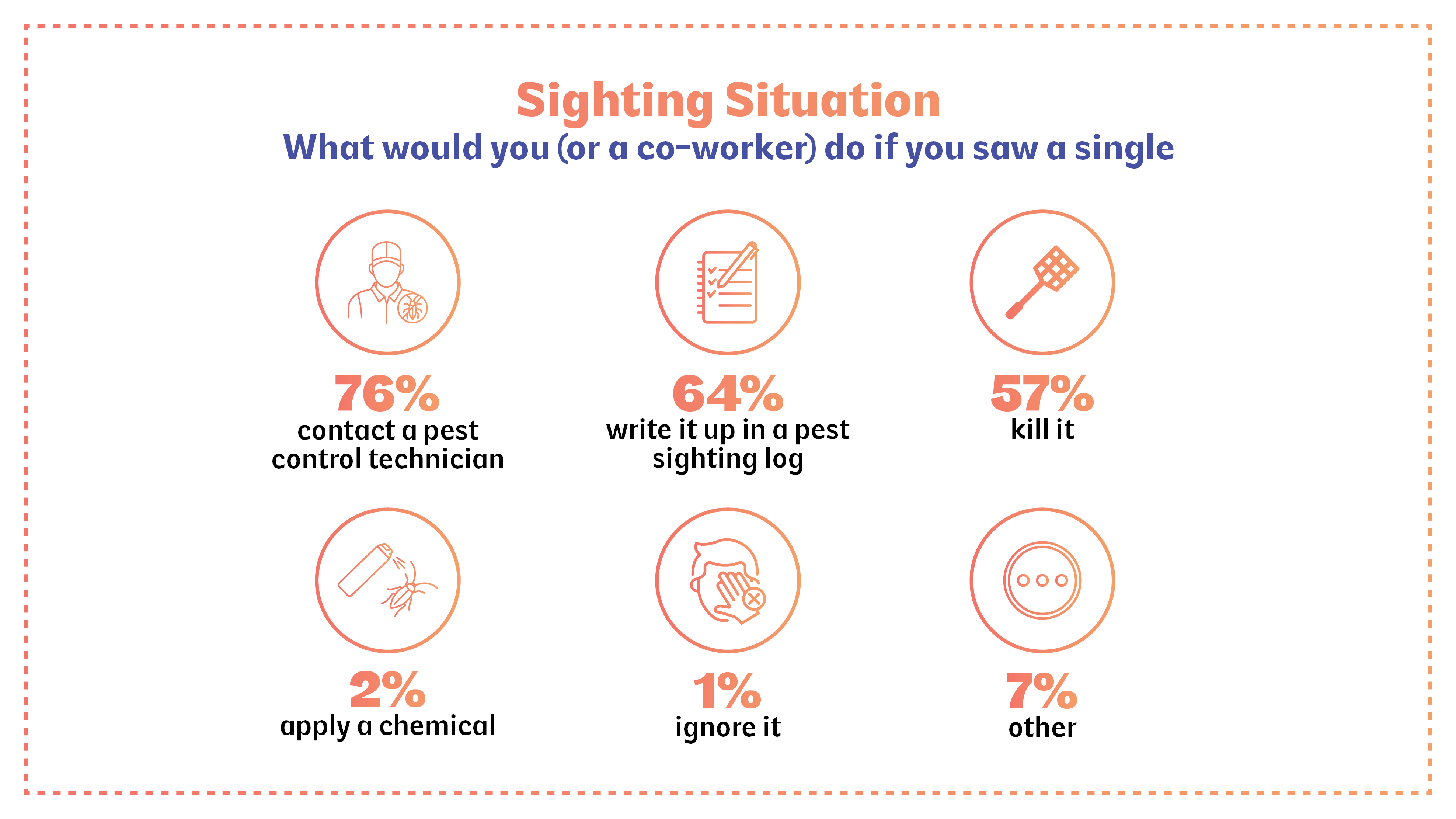
Maintain a logbook and regularly emphasize this tool to employees in the facility.
“Notes in logbooks in real time can prevent employees from forgetting sightings and other information that could help guide the PMP,” Crawley said.
Hottel added, “Documentation should be easily accessible with the ability to track and trend pest populations.” She advises quarterly and annual assessments to “provide an opportunity for team synergy.”
Hate to admit your facility didn’t exactly follow the pest control company’s recommendations? “Don’t fabricate or over-inflate actions you’ve taken,” Crawley said. “It only stalls progress.”
Connect with the technician performing service, Hartzer said. “Ask them what is going on, look at the reports and ask what you could be doing to make a situation better. Even a five-minute conversation can give you huge amounts of information.”
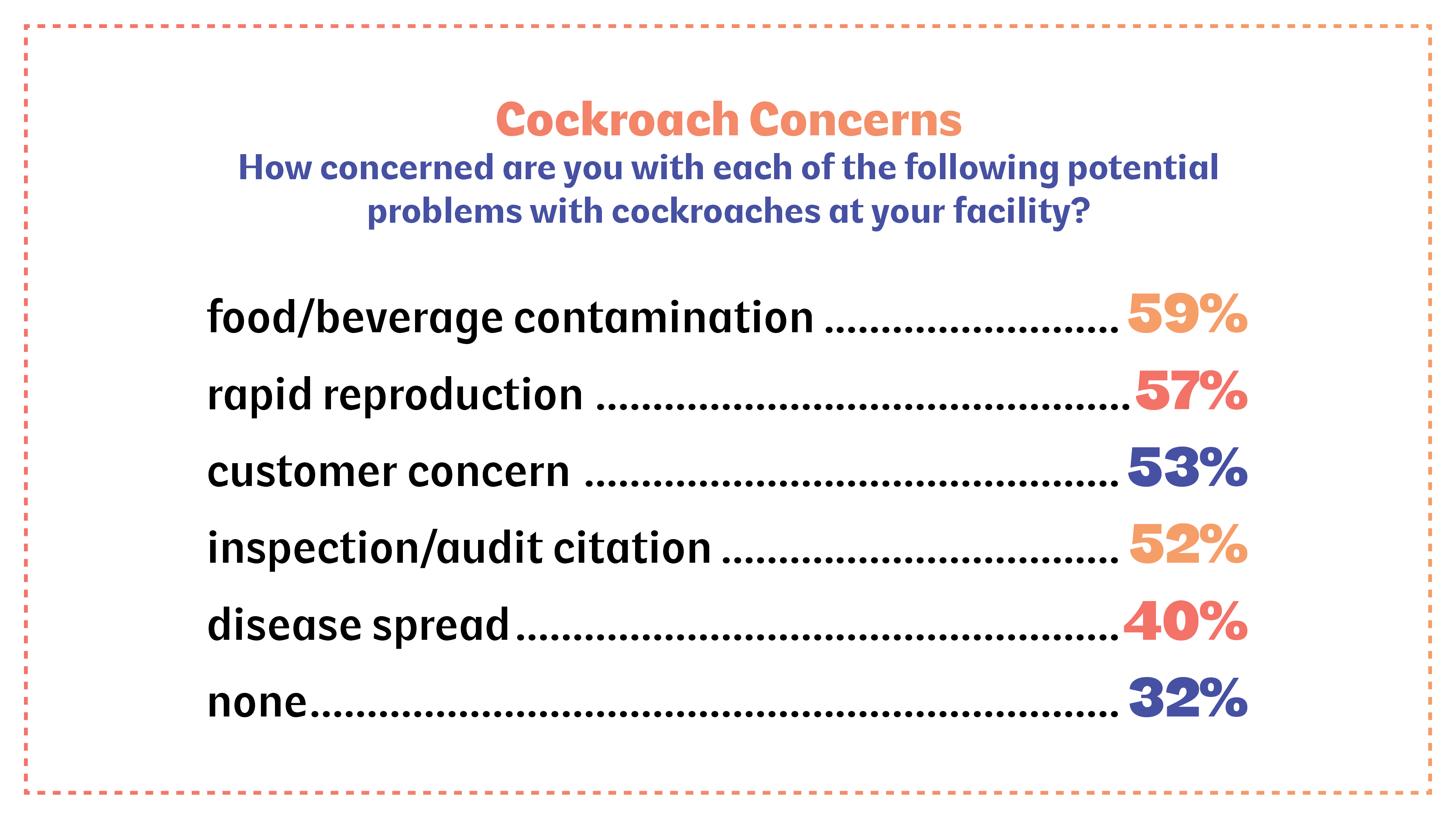
SEEK OUT TRAINING. Incorporate pest identification training in team meetings and find out if your pest control provider can lead some training sessions. Hottel has delivered training at food processing facilities to communicate every employee’s important role in maintaining a sanitary environment.
“We make sure they know what to look for and how to report sightings, along with steps they can take to prevent cockroaches and what conditions are favorable to cockroaches,” she said.
Along those lines, establish protocols for employee breakrooms and lockers. “Emphasize the role employees play in transporting pests from homes without realizing it,” Hottel said.
QA survey respondents cited these two areas of their facilities as hot spots for cockroaches, with 53% finding the pest in an employee breakroom or kitchen, and 27% noting pressure in and around employee lockers.
“Since the German cockroach can commonly be introduced via employees’ personal belongings and lunches, having less cockroach-friendly refrigerated storage cases can be useful,” Hottel said, also recommending scheduled locker and lunch storage area clean outs. “This is when employees must empty their lockers and remove all food items in the break room during a pre-scheduled weekend. Lockers and areas are then inspected for pests and cleaned.”
Ultimately, successful collaboration requires getting everyone on board.
“It takes a diverse team on both sides to discuss how to make program improvements, so make sure you are involving team members from the pest management provider — including technical directors and specialists — and operations managers,” Hottel advised. “Include facility team members such as maintenance, sanitation, food safety and plant management. Everyone’s presence is important.”

Explore the March/April 2024 Issue
Check out more from this issue and find your next story to read.
Latest from Quality Assurance & Food Safety
- Martin A. Makary Sworn in as FDA Commissioner
- Cargill Kitchen Solutions Recalls Liquid Egg Products Due to Unapproved Substance
- Eagle Product Inspection’s PXT and SimulTask PRO Integrate for Contaminant Detection
- Boar's Head Appoints Natalie Dyenson as Chief Food Safety Officer
- West Virginia Bans Seven Food Dyes
- Seeding The Future Global Food System Challenge Finalists Revealed
- TraceGains Launches AI-Powered Intelligent Document Processing to Improve Ingredient Safety, Compliance
- IFT Virtual Workshop on Food Fraud Prevention to Address Supply Chain Disruptions