Editor’s Note: Having been “on both sides of the fence,” the author provides his insights on and recommendations for audits, particularly as related to pest management.
By Al St. Cyr
The pest management industry would appear to be entering into another age of countless opinions on how programs should be designed and implemented for food facilities. Unfortunately, these opinions are often coming from people with little or no expertise or practical experience. Hardly a week goes by that I do not get a call for advice on what a third-party individual is demanding be done at a food account. Far too often, the search for advice is not based on interpretation of an audit standard but solely on the opinion of an individual auditor. Unfortunately, not many customers will question the “opinion” of the auditor for fear of retribution.
A sad part of this is that people who audit or inspect facilities are supposed to subscribe to a code of ethics to follow the designated audit criteria or standard, and not deviate or inject their own personal biases. Having been an auditor, I admit this can be difficult at times, but that is what discipline is all about. It appears that the field of pest management has become a particular target for some individuals who lack knowledge and skills in pest management.
The true and respected professionals in our trade invested long hours to accumulate a vast knowledge of science-based, practical experience to improve their understanding of many industries. They have learned from their own and other people’s mistakes to try to make sure the failures are a teaching moment, not repeated. It is hard to pinpoint exactly when this acquired knowledge began being replaced by non-substantiated opinion.
THE SCIENCE OF PEST MANAGEMENT. What concerns me is that the pest management industry is coming under increasing pressure from groups that have absolutely no knowledge or understanding of the science of modern pest management. More concerning is their refusal to seek the counsel of recognized industry experts. Far too many times, I am baffled by where these groups acquired their information or how, exactly, they formulated their policy. How did totally non-related and anecdotal bits of information suddenly become linked together and expressed as fact?
Let me reference a few examples:

- A state investigator recently cited a client, who was using pheromone traps to monitor for stored product pests, with improper storage of a pesticide leading to contamination of food products in the warehouse. It was said that since the pheromone was a volatile material, it was contaminating food products (in packaging) around each trap. This investigator insisted the traps be removed and the food items evaluated for disposal.
- An auditor failed a facility for having placed mouse snap traps with a common commercial attractant in a warehouse rack system where a mouse had been reported as being seen. The auditor said the use of baits in a food facility was illegal (not so according to rodenticide labels) and the traps would only work if they were placed along the wall. The facility’s request for review was denied.
- According to another auditor, FSMA requires that a facility have copies of the résumés for the pest control company owner, branch manager, immediate supervisor, and technician working in the facility. Their reasoning is that we need to prove every person involved in the pest control program proves his or her competence. A statement was made by the auditor that pest management is now a preventive control under FSMA rather than a prerequisite program. I fail to see what a résumé has to do with proof of competency or understanding of the job. I would have thought the state-issued license, NPMA QualityPro certificate, and NPMA GMP exam certificates would have sufficed. Nope, new rule with this auditor is résumés. (By the way, IPM is a prerequisite program.)
- Patio blocks can no longer be used to secure the stations because someone can pick it up, take it home, break into it, and get the bait. They have to be bolted to the building or staked to the ground. Past experience tells me that these are the two least favorable options. The industry secured the bait inside the station to prevent children and animals from shaking out the bait. When attached to a foundation, the stations will just get higher and higher as the ground around the plant sinks. As one facility manager said, “I just spent $450,000 to pour concrete around my facility, and now you are telling me I have to let you drill holes every 50 feet?” Yup. The auditor told me I had to.
- Every bait station has to have a “Poison” label on it because everything used in them is poisonous. Apparently, this person is not familiar with non-toxic monitoring blocks that are an integral part of a proactive preventive monitoring program, and is a system commonly used for organic and LEED facilities. PR Notice 94-7 simply requires a station be capable of displaying a “Precautionary Statement.” Some states have rules about identifying the rodenticide contained in the station but not all. These stations were labeled as “Toxic Bait” or “Non-Toxic Monitor” to reflect what is in them. But that was not good enough for this auditor: Label all as poison regardless of what is in it.
- This one stopped me dead in my tracks: An auditor said, “You have to have the bait stations directly on the ground against the wall so the rats can find the hole in them because rats are blind. Up on patio blocks they will never find them.”
- If you are having a BRC audit, all of your equipment must conform to British rules and regulations because the BRC is a British audit. The bottom line is that the auditor simply did not like the particular bait station the company was using. It was fully compliant with EPA requirements and each was appropriately installed.
- Everyone has his or her own nightmare stories about the sad requirements some people have tried to place on pest control in food plants, but having to build a platform at each side of a third-story roll-up door used once a year during deep maintenance, so that bait stations could be installed at each side of every exterior door of a facility, kind of topped them all.
ENOUGH IS ENOUGH. Pest management and food safety professionals: say enough is enough. Read and learn the criteria being used to inspect/audit your facility. When auditors are clearly injecting their personal opinions on an issue, demand they show cause in the audit criteria. If it does not make sense to you, question the validity of what they are telling you to do. Show me the science or regulation please.
I recall a time when inspectors were chosen from a field of people who had a track record of success and an ability to teach. It was an honor to be asked to join the ranks of a recognized organization with a history of success helping companies grow and succeed. Even though many of the audit schemes specify the number of years a person must have in a given industry before he or she can officially audit a firm in that category, it would appear that, today, a piece of paper stating so will do.
Many competent pest control companies spend considerable resources of money and time to train their technicians to work in the food industry. We maintain licenses as required by the states we work in and must maintain continuing education to retain them. How many auditors can say the same? The reality is that, in the state of California and others, you have to have a license to legally identify pests and make recommendations for a control strategy. The sad truth is that very few auditors have invested in learning science-based pest management and acquiring the credentials permitting them to do so.
Like the food industry, the pest management industry is far from without fault. Both industries need someone looking over their shoulders to help keep things on track. During recent years, there has been a significant loss of common knowledge about pest management strategies and what is needed in a food plant. This seems to have fostered a sense of animosity rather than cooperation.
There are many dedicated and informed auditors practicing their trade. Many of them also scratch their heads at some of the edicts coming down from the armchair experts. Collectively there needs to be an open forum to discuss ideas and concerns. Priorities are the concerns for the safety of the consumer and the integrity of the food products. Keep this in mind and use a little common sense, and we should all be fine. The one who has the most number of devices in the end is NOT the winner. The one with a well-thought-out, risk-based program free of any pest activity is.
I would strongly suggest the audit groups and their entire staff acquire a copy of the National Pest Management Standards for Food Processing and Handling Facilities . This document outlines accepted approaches for pest management in any food handling establishment. It is a guidance document that should be used to meet the established criteria of an audit scheme rather than simply using the opinion of an ill-informed auditor who may change his mind frequently.
The author, who is President of ASC Consulting, was formerly with a food industry auditing organization.
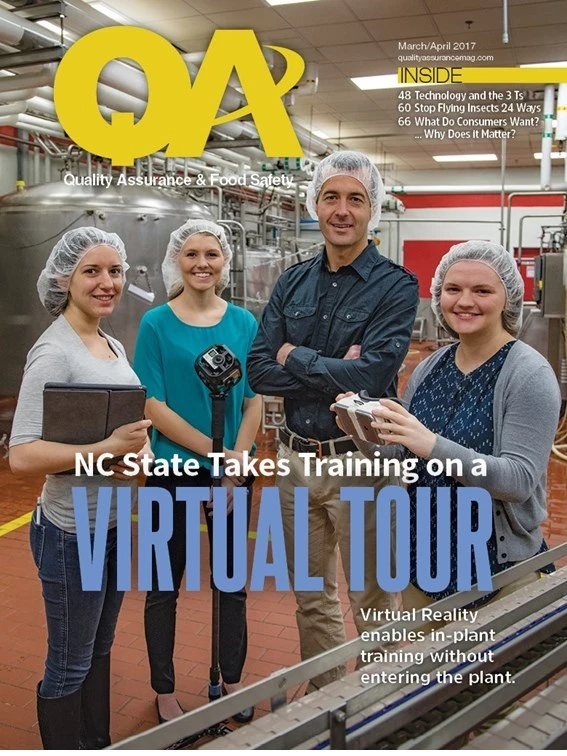
Explore the April 2017 Issue
Check out more from this issue and find your next story to read.
Latest from Quality Assurance & Food Safety
- CSQ Invites Public Comments on Improved Cannabis Safety, Quality Standards
- Registration Open for IAFNS’ Fifth Annual Summer Science Symposium
- Leaked White House Budget Draft Proposes Shifting Inspection Responsibilities from FDA to States
- Chlorine Dioxide: Reset the Pathogenic Environment
- Ferrero Group Invests $445 Million in Ontario Production Facility
- Nelson-Jameson Announces Grand Opening for Pennsylvania Distribution Center
- Taylor Farms Linked to Romaine E. coli Outbreak as Marler Clark Files Multiple Lawsuits Against Supplier
- IAFNS Announces Winners of Emerging Leader Awards for Food Safety, Nutrition