Although initially seen by many as a detriment to the protection of stored grains and seeds, the phase out of methyl bromide is bringing with it new trends and developments in fumigation and stored product pest control alternatives. Most notable are the increased focus on integrated pest management (IPM), with particular emphasis on prevention; the adherence to organic and natural practices; and developments in fumigation products and tools.
IPM FOR PREVENTION. “Preventing the need for fumigation is an extremely worthwhile strategy,” said Copesan’s Director of Technical Support and Regulatory Compliance Jim Sargent. “To paraphrase Ben Franklin, an ounce of pest prevention is better than pounds of fumigant.
“That’s not saying that a food plant can avoid ever needing a fumigation,” Sargent added. “But a food plant can reduce the need for an expensive fumigation by investing in a comprehensive IPM program.”
Dave Mueller, owner and president of Insects Limited, and owner of Fumigation Service & Supply, agreed. Fumigation is still needed, but it is no longer being used as a crutch as it had too often been in the past, he said, with a pre-set schedule of Memorial Day, Fourth of July, Labor Day fumigations — whether it was needed or not. Instead, Mueller said, “we just started doing all the things we were supposed to be doing.” Things such as the preventive practices of IPM, sanitation, exclusion, product rotation, inbound inspections and monitoring.
Many processors have significantly increased their focus on exclusion, said Stephen Roy, executive director of the Food Protection Alliance, a network of regional companies with particular expertise in fumigation. “The component that has evolved is that companies are recognizing that they can take fumigation dollars and put them into their structure.” Building out insects by enhancing the soundness of the structure and sealing cracks and crevices not only helps to exclude insects, but also enhance efficacy if a fumigation is needed — by reducing gaps, holes or crevices where insects could come in or fumigant could leak out.
The current organic trend also is contributing to increased integrated pest management practices, Roy said. Even if they are not producing an organic item, he said, “many companies are trying to adopt the philosophy and minimize fumigation.”
'A WORLD OF ODOR.' Product rotation is important, Mueller said, because insects “live in a world of odor.” Even if they appear to be sound, products that are two or three years old emit a different odor than do new products, and this odor can attract the female as an ideal egg-laying area. She will seek the oldest lot in your warehouse then drop her eggs at night to hatch and subsequently infest your stored goods.
The additional step of monitoring with pheromone traps can be an excellent preventive measure to detect and pinpoint insect presence, enabling control measures to be taken early. If even the start of an infestation is detected, Mueller said, you should throw away the product, fumigate surrounding product or goods, place more monitoring traps, quarantine the area, fog and double fog — “at that point you do everything!”
Incoming goods can be a significant problem area if suppliers are not held to strict requirements and goods not inspected upon arrival. “Thorough sampling and inspection of incoming grains and ingredients is possibly the most important tool in the IPM toolbox,” Sargent said. “If live insects are found or if the quality isn’t there, don’t bring the commodity into your facility to compromise the quality of everything that is shipped from the facility. As the saying goes in the computer world, ‘garbage in, garbage out.’”
Adding such focus to inbound materials benefits the quality of the entire supply chain, Roy said, explaining that when a processor spends the extra dollars needed to manage its input in the same way as it manages its output, it “minimizes the risk to the entire process.”
“Many people are requiring the ingredients be fumigated in transit,” Mueller said, adding that in the U.S. alone 60,000 railcars are fumigated every year with phosphine. Adding better inspection of all incoming goods at the receiving dock along with lab sampling of by trained personnel, he said, “provides added insurance that everything possible is being done to bring a pest-free product to the consumer.”
STILL A NEED FOR FUMIGATION. Even with the alternatives and emphasis on prevention, there can still be a need for fumigation. In fact, Sargent said, “It’s ironic that one kind of prevention strategy may include fumigation.”
Today’s fumigations can be more costly and time-consuming than in the past, as they include an increased emphasis on sealing, a greater need for planning of the fumigation further in advance, more monitoring — inside and out — and more regulations to keep up with. However the availability of better sealing materials and products and more knowledgeable fumigation professionals are also resulting in generally better fumigation treatments, resulting in high quality pest control.
There are more and more regulations impacting fumigants today, Sargent said, many of which have been enacted since Sept. 11 and focus on security. “People get nervous when you say you’re using an odorless, colorless gas that’s very toxic,” he said.
METHYL BROMIDE PHASE-OUT. The regulations that have impacted the use of the previously popular fumigant, methyl bromide, go beyond the U.S., having been identified as an ozone-depleting substance by the 1989 Montreal Protocol. While methyl bromide was scheduled for elimination by 2005, the act included an allowance for critical use exemptions, of which the U.S. has taken full advantage.
“The U.S. itself has asked for more exemptions than the whole rest of the world combined,” Mueller said. Although alternative and newly introduced fumigants have proven to work as well as or better than methyl bromide, “people don’t like change,” Mueller said. “People don’t like to lose tools from their toolbox.” In fact, the U.S. has applied for critical exemptions for the use of 6,500 tons of methyl bromide in 2008 and 5,000 tons in 2009 — more than that of the rest of the developed world combined at 1,900 tons for 2008 and 1,400 tons for 2009, including both non-soil and soil fumigations.
“Why are we still using it?” Mueller asked. “Methyl bromide is a serious ozone depleting substance. We’re being ridiculed by countries all over the world.”
One of the most significant alternatives identified by both Mueller and Sargent is ProFume gas fumigant, a sulfuryl fluoride product. Manufactured by Dow AgroSciences, ProFume was federally registered in 2004.
“There are still some important uses for methyl bromide for which there are no economic or effective alternatives,” Sargent said, such as those not yet on the ProFume label or certain farm soil treatments. “So we don’t want to lose it completely from the IPM toolbox.”
PROFESSIONAL APPLICATION. Use of ProFume requires minimal change from the standard industry practices of methyl bromide, and, as a restricted-use product, still requires treatment by a certified professional. When contracting with a third party for the fumigation, said Dow U.S. marketing specialist Jason Nelson, the processing plant should ensure that the professional fumigator:
- be fully trained in and understand current pest management practices, including all proper application techniques and safe-handling practices.
- incorporate state-of-the-art technology.
- implement IPM practices that include fumigation as a tool.
- have access to manufacturer support and expertise.
- have an understanding of a facility’s special needs, gained primarily through pest monitoring.
- ensure efficacy based on monitoring.
In addition to applicator expertise, exclusion practices and improved fumigation sealing have become even more important to the fumigation process, Sargent said. The benefits of sulfuryl fluoride also can be a negative, in that, he said, “Sodium fluoride penetrates better, but it also escapes better.” So if a building is not tight, the chemical can penetrate out of the structure as well as it can penetrate into the infested commodity.
OTHER DEVELOPMENTS. New research and development in the area of stored product pests and fumigation are bringing more effective and efficient treatments to the table. Much of which is being made possible by precision fumigation techniques, new fumigants, better delivery methods and monitoring systems designed to deliver useful information — not just more data, Roy said.
A significant continuing development in fumigation is remote monitoring.
Though not a new technology, “there are big advances being made in remote monitoring,” Roy said. The technology allows the customer or government to remotely sample the gas while a fumigation is being performed. While monitoring itself is not new, there is aggressive work going on in the area to improve and expand on the technology.
In addition, a biosensor is being developed by Insects Limited and Purdue University that is able to detect if insect eggs are still alive in a fumigated area by remotely measuring their oxygen output. It’s much easier to kill insect adults, Mueller said, but the eggs and pupae breathe slower and take in less fumigant over time. “If we can measure the mortality of beetle and moth eggs, we should start getting better fumigations in flour mills and other food processing structures,” he said. This biosensor concept was patented and publicly presented by Dirk Maier of Purdue University in October. Mueller expects it to be on the market within one to two years.
While fumigation will always be necessary in some applications, increased attention to IPM, product rotation, incoming goods inspections and supplier requirements can help prevent insect infestations before they can begin, while the increased knowledge and developments in fumigation itself are continuing to make this treatment more efficient and effective.
The author is Staff Editor of QA magazine.
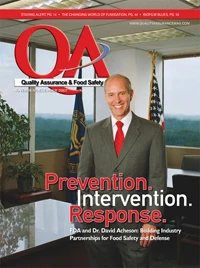
Explore the December 2007 Issue
Check out more from this issue and find your next story to read.
Latest from Quality Assurance & Food Safety
- FSIS to Host Virtual Public Meetings on Salmonella Framework
- Climate-Smart Soybeans Enter U.S. Market
- Yoran Imaging Introduces Thermal Imaging-Enabled System for Induction Seal Inspection and Analysis
- GDT Highlights Food Safety Solutions for Food Processing and Packaging Facilities
- FSIS Issues Public Health Alert for Ineligible Beef Tallow Products Imported from Mexico
- Wolverine Packing Co. Recalls Ground Beef Products Due to Possible E. Coli Contamination
- McDonald’s USA, Syngenta and Lopez Foods Collaborate to Help Produce Beef More Sustainably
- Divert and PG&E Announce Interconnection in California to Address Wasted Food Crisis