In late January of 2009, one of the largest and most expensive food recalls in the history of the United States began when officials from the Food & Drug Administration (FDA) learned that Peanut Corporation of America (PCA), headquartered in Lynchburg, VA, had shipped peanut-based products contaminated with Salmonella bacteria 12 times in 2007 and 2008 from its Blakely, GA facility. This was a clear and significant violation in food processing standards. Yet, what compounded this problematic and potentially dangerous situation was a single fact: a Salmonella outbreak was occurring nationwide and the FDA was in search of the source – a source that this discovery provided.
With numerous reports of Salmonella poisoning flooding the Centers for Disease Control (CDC), a deeper investigation into PCA commenced in late 2008. By early winter 2009, a startling and disturbing picture of PCA’s food manufacturing processes was publicly painted, specifically in Blakely, GA. From mold growing on ceilings to rainwater leaking into the production areas; from gaps large enough for rodents to easily access the facility to the presence of dead cockroaches throughout the plant, the conditions were termed unsanitary and harmful by FDA. Beyond these conditions, e-mails between company executives demonstrated knowledge of these conditions and more critically, acknowledged the positive tests for Salmonella within products over a two year period. These positive tests came from PCA products linked to the national Salmonella outbreak – an outbreak that ultimately led to more than 700 cases of Salmonella in 46 states and nine deaths.
The conditions and day-to-day processes of PCA’s Blakely, GA plant were deemed so poor that the FDA made an unprecedented request in its recommendation to recall more than 400 peanut products, ranging from snack crackers to ice cream to dog biscuits. In its January 29, 2009 statement, the FDA asked all retailers, manufacturers and consumers to discard any and all peanut products processed by PCA dating back two full years to 2007. Such a massive recall affected numerous, highly visible brands that had used PCA as a supplier, notably Kellogg, McKee Foods, Ralcorp and Trader Joe’s, and created more that $1B in lost sales for these companies.
From that particular moment, the issue of safety within food facilities became a front page story. As additional details about PCA’s Georgia plant became public and as similar – if not worse – details regarding its Texas facility emerged, government officials and consumers were equally outraged and the discussion of whom to blame, the cause of the outbreak and how such problems could go unnoticed and unaddressed reached a fever pitch.
Yet in a full year since the outbreak, the fever pitch has died down quite a bit, leaving us with an important question: Where do we stand in preventing such an outbreak – and such a clear breakdown in food facility safety practices – from reoccurring?
Although the media scrutiny and public conversation regarding the salmonella outbreak have lessened dramatically since spring 2009, the story continues. Here are just a few actions that have occurred or are currently underway in relation to this issue:
- Peanut Corporation of America filed for Chapter 7 bankruptcy protection and has been liquidating any/all assets since February 13th as civil claims against the company continue to mount. These claims have not only been filed by individuals affected by the Salmonella outbreak, but also by those companies and brands that were supplied contaminated peanut products.
- The U.S. Attorney’s Office continues to investigate PCA and its executives, with the potential for criminal charges still to be brought, especially as the e-mails between President Stuart Parnell and Sammy Lightsey, Manager of the Blakely, GA plant, reflect knowledge of the presence of Salmonella and discussion about whether to supply potentially contaminated products, which PCA did. With multiple deaths and hundreds of serious illnesses related to the outbreak, this case remains open and active although no charges are currently pending.
- In November 2009, a Senate committee approved for full discussion and voting the Food Safety Modernization Act of 2009, which would require the FDA to inspect food-processing plants at least once every four years. However, plants that handle high-risk foods will be inspected each and every year. Further, it would not only require all food manufacturing plants to have safety programs in place but also grant the FDA the power to instigate mandatory recalls of products. Currently, the FDA can only encourage companies to make voluntary recalls unless it takes the step of obtaining a court order. The House of Representatives has also passed a similar bill with significant differences, notably with regard to frequency of inspection, which will need to be reconciled before it can be passed.
Certainly, these actions could prove beneficial in strengthening food safety standards and may serve to prevent future outbreaks. Yet, these do not necessarily address the central issues as to why this outbreak may have occurred. Yes, there were clear errors made by PCA in creating this situation but to lay full blame does not serve the public or those individuals, firms and agencies responsible for food safety well. This situation showed a need for comprehensive review and perhaps reforms in the way that food safety practices are implemented, audited and reported. And in reviewing the “red flag” conditions that appeared in the FDA’s investigation of Peanut Corporation of America, it became clear that the professional pest management industry needed to be consulted and could help determine the necessary “next steps” toward preventing this type of outbreak and recall situation from reoccurring. It also became clear that food manufacturing facilities need to work in strong partnership with professional pest management firms moving forward.
Pest Management in Food Manufacturing Facilities: Its Necessity and Its Obstacles
In reviewing the issues arising from PCA, it should be clearly stated that pest management practices – or lack thereof – were not the central cause for the nationwide Salmonella outbreak. Yet, when one considers the presence of such conducive conditions for pests, the presence of cockroaches throughout the facility and the simple fact that Salmonella, was transmitted – a disease for which rodents can so often be a vector – poor or improper pest management practices could be viewed as a contributing factor in creating this crisis situation.
In the absence of a singular cause for the Salmonella outbreak and in light of the havoc caused by a national recall of PCA products, the situational details reflect the need for strong, effective and consistent pest management practices within food facilities. The illnesses, and ultimately the fatalities, associated with the outbreak serve as an important reminder that food safety cannot be taken for granted in the United States. Corporations must give the requisite time and attention to maintaining food facilities or human health – not just product – can be adversely affected.
The presence of pests – dead and alive – in the Georgia PCA Plant is also a reminder of the significant health risks associated with pest infestations. No matter the size or severity of an infestation, a pest problem is not a situation to be taken lightly. Cockroaches, rodents and other pests are known to transmit diseases, including Salmonella, which is carried and spread simply on the body and hairs of pests.
With such knowledge of the potential health threats related to pest infestations, it is inconsistent that there should be any obstacles to the implementation of a strong pest management program. Yet, as the PCA situation proved – and as many firms can likely attest – pest management often faces challenges in asserting its rightful place among “top priorities,” for corporations. These challenges, well-recognized within the industry, may have contributed to the PCA crisis in ancillary ways. Yet, regardless of how large or small their underlying role in this crisis, these challenges should be addressed and discussed as government, corporate executives and food facilities work to strengthen future oversight initiatives. If there are to be forthcoming changes in how food facilities are inspected, audited, evaluated and treated then it is critical that three particular challenges related to pest management – that of organizational priorities, clarity of standards and service benefits - must be more deeply discussed within the context of a post-PCA world.
Pest Management: A Secondary Issue
In food manufacturing, pest management is accepted as a necessity. Yet, in practice, when every penny and every moment must be spent strategically, the necessary financial and time commitment to proper pest management tends to fluctuate. The critical importance of pest management is often minimized and even “rationalized away” when there are decisions to be made regarding day-to-day operations. Yet, a consistent focus upon developing a strong pest management program – a program that includes regular inspections and audits, proactive pest-proofing measures and immediate action when facing a potential infestation – is essential to providing consumers with safe and healthy food products.
A willingness by corporations to view pest management as anything less than a top organizational priority can lay the groundwork for significant future problems. Although efficient – and even increased – production is the central goal of any food facility, this goal cannot be met at the expense of consumer safety. Corporate executives and food facility managers must ensure that all links within the food safety chain are properly maintained, with pest management as an important link in this chain. Pest management, especially in a food facility, should not be a line item that is shifted, reduced or simply cut when other business issues arise, as it plays a vital role in protecting the health of consumers. That alone is a compelling reason for facility managers to make a strong financial investment in proper pest management.
Yet, it is that financial investment in proactive pest prevention which often relegates it to a second tier business priority. When that particular investment is compared to the investment necessary for manufacturing machine maintenance, employee salaries and benefits, increased commodities costs and other business issues related to a food facility’s goal of efficient production, pest management often shifts further down the list of priorities. And the further it slips, the greater the chances that a situation similar to PCA’s will develop.
It also should be noted that the emergence of Salmonella at the Blakely, GA plant coincided with a dramatic downward spiral in the U.S. economy – a spiral, which saw many corporations making drastic cost-cutting measures. Of course, the issues of PCA ran far deeper, dating back to 2007, when the economy was booming. However, general economic factors must be considered when analyzing possible methods of preventing similar situations.
Even with the economy factored in, pest management should emerge from the PCA crisis being viewed as a top priority by government, corporations and decision-makers alike, especially for those in food manufacturing. Strong pest management practices can often lay the foundation for overall “best practices.” When food facilities understand the threats posed by pests, acknowledge the significant contamination risks and fully recognize the value of being proactive in pest management, they can then achieve the benefits of operating at their safest and ultimately most efficient production levels.
Ambiguity within State and Federal Standards for Pest Management
One of the reasons for such public and governmental outrage surrounding PCA was the fact that their facilities passed regular inspections. This highlights another issue consistently discussed within the pest management industry regarding the inspection and treatment of food manufacturing facilities -- the level of ambiguity often inherent within the state and federal inspection standards.
In an effort to not dictate the way in which food facilities implement pest management programs (or other food safety programs for that matter), there is a lack of specificity as to what constitutes a proper, thorough and ongoing program. For many corporations and food facilities, there is a tendency to view standards and statutes as guiding principles – principles that provide a framework for a pest management program but do not necessarily need to be strictly followed. Within the pest management industry, existing standards and statutes represent the bare minimum of what should be done with regard to pest management in a food facility. And in many situations, pest management firms find themselves advocating for enhanced services due to the frequency, scope and importance of properly treating food facilities. This view of standards, especially if coupled with a view of pest management as a secondary issue as previously discussed, can often lead to a disconnect between food facilities and pest management professionals.
For pest management programs to be effective in protecting the food supply and protecting consumers, standards must be clear and enforced. For so long, ambiguity of standards has allowed food facilities and pest management professionals to seemingly operate almost separately of one another. Yet, with scrutiny upon the inspection process after PCA, the focus is now not simply on meeting standards but encouraging food facilities to exceed them. However, to achieve this, standards must be more clearly articulated for both parties so that all can speak the same language when discussing the role of pest management in food safety and prescribing the proper program for prevention and treatment.
Should the Food Safety Modernization Act of 2009 pass the full Senate and be signed into law, this piece of federal legislation would take significant steps in transforming food safety in the United States. Beyond the additional recall power it would grant the FDA, this law also addresses the need for increased inspections of food facilities and increased reviews of previous inspection records. Not only would inspectors be more empowered to ask questions through this legislation but also, could provide food facilities with clearer direction in implementing safety measures, including pest management programs, to meet national food safety standards. Such clarity in standards could allow food facility executives to better understand the value of pest management in protecting its food supply. Further, the requirement for increased inspections may encourage more consistent and open communication between pest professionals and facility managers regarding emergent pest issues within a food facility.
The absence of an effective pest management program was one issue at the heart of the PCA crisis with the issue of standards as a contributing factor. By working to better understand health and safety standards, especially as they relate to pest management, food facilities can position themselves well to meet these and any enhanced standards that may result from the PCA crisis. When addressing pest management standards, though, it is likely wise for food facilities to outreach to a professional pest management firm that can help managers to fully comprehend the expectations for compliance and work to develop proactive, realistic and effective programs that meet all standards.
Proving Preventative Pest Management Works
When pest prevention is done well, it leads companies – and food facilities, specifically – to believe that they do not have pest problems and thus, do not need ongoing pest management services. However, there is rarely the recognition that the lack of pests is due to the consistent and effective pest management services being provided. When pest professionals are given access for in-depth inspections and the ability to communicate with organizational decision-makers regarding their findings, concerns and recommendations, many of the issues that plagued PCA rarely arise. In fact, it is when a true partnership is cultivated between a pest professional and executives at a food facility that prevention is at its best.
Yet, as logical as that may seem, it is not yet the norm. In fact, facility managers are often faced with making the increasingly difficult argument to corporate executives that prevention measures are the direct reason that the facility does not have a pest problem.
In reality, the pest infestations that arise after companies forgo proactive prevention measures tend to wreak far more havoc and cost to treat than the prevention program that may have staved off such pest problems. PCA is an outstanding example of that. Not only did the lack of preventative measures lead to food contamination and illness but more, it led to a public outcry against the company for its blatant disregard of meeting proper safety standards.
A defunct level of commitment to pest management is likely to be a reflection of the overall corporate view toward safety. It was true of PCA and in its wake, food facilities have been left to reevaluate their own programs and try to find ways in which to strengthen safety measures and allay consumer concerns. Preventative pest management is just one way in which to do this, especially if pest professionals can work with facilities to help them understand the long-term benefits of preventative maintenance.
A Final Note
While there will likely be future outbreaks and product recalls, the Salmonella outbreak of 2009 may very well be reflected upon as a turning point for food safety in the United States. Although there were extensive mistakes, poor decisions and missed opportunities for oversight that led to the crisis involving PCA, these miscues provide an opportunity to strengthen the food safety process nationwide. With lessons learned, food facilities must reevaluate what safety means for both their consumer and their business. Pest management is an important piece in addressing the safety of both. As such, there must be a reevaluation of the role that proactive pest management currently plays within the manufacturing process and if necessary, a recommitment to supporting this particular safety measure by company executives and food facility managers. No longer can pest management be relegated to a secondary priority or can it fall through the cracks of misunderstood standards. The PCA crisis compels food facilities to reprioritize so that safety truly is first. One way in which to do so is to focus renewed efforts on implementing proper pest management programs.
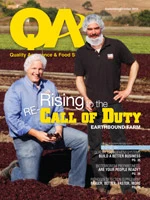
Explore the October 2010 Issue
Check out more from this issue and find your next story to read.
Latest from Quality Assurance & Food Safety
- Taylor Farms Linked to Romaine E. coli Outbreak as Marler Clark Files Multiple Lawsuits Against Supplier
- IAFNS Announces Winners of Emerging Leader Awards for Food Safety, Nutrition
- FDA Shares Testing Results for PFAS in Bottled Water
- Provision Analytics Adds Food Safety Expert Jennifer Williams to Strategic Advisory Group
- Boston Sword & Tuna Protects Seafood Safety with Mettler-Toledo Metal Detectors
- IFT Releases New Resources to Aid Food and Beverage Industry in Sugar Reduction
- Yum! Brands CEO David Gibbs to Retire in 2026
- Penn State Extension Offers Short Course on Food Microbiology and Safety for Food Plant Workers