Over the last two decades, the food industry has undergone change in a big way. Major food safety regulations and programs have been initiated, but recalls still seem to occur frequently (with social media highlighting every one). The problem isn’t just in the food industry. Vehicles are being recalled in their first few years; artificial hips, heart valves, and other medical products are recalled on a regular basis; toys are notoriously high on recall lists.
But it is the food industry that is seeing heavy regulatory change: About 20 years ago, USDA’s Food Safety and Inspection Service (FSIS) added a regulation to consider raw ground beef contaminated with E. coli O157:H7 as adulterated within the meaning of the Federal Meat Inspection Act; 14 years ago, the Global Food Safety Initiative (GFSI) was started; and four years ago the Food Safety Modernization Act was signed into law.
Are food contamination issues caused by profits being put ahead of quality assurance, food safety, and other non-profitable yet essential responsibilities? Not likely, as this strategy is not good business. Rather, I would suggest that too many regulations, too many requirements, and too many programs are too much to deal with, stress company resources, and are simply not practical. The food industry is being challenged to provide safe, wholesome products at the lowest possible price. Are we past fundamentals? What is a practical QA solution?
Determining the Problem. The solution must come from the board room. Vision, mission, and core values can create some nice sounding words. But if quality assurance and food safety are not also in company guidance documents, there may be a leadership problem. If quality assurance and food safety are included, then the problem may be commitment. Commitment must come out of the board room represented by a quality assurance culture making decisions backed by adequate financial and human resources. If quality assurance and food safety are being given sufficient financial and human resources, then the problem may be management or incentives. If the board room is committed, but this is not being seen in employee actions and decision making, then there is a flaw in the organization’s system.
The Solution... should be reflected by the organization’s structure. Quality assurance and food safety are closely related as they work hand in hand. There are a number of ways to structure quality assurance and food safety, but regardless of the structure, a quality assurance culture must be reflected in the company’s organization. Additionally, there are good ways to accomplish checks and balances. But an ugly way is when an organization allows quality assurance decisions to be vetoed by production or manufacturing. At the corporate management level, the structure may have quality assurance report directly to the owner or CEO (e.g., by having a vice president of quality assurance) or indirectly (e.g., having a director of quality assurance report to a vice president of technical services).
When there are two supervisory levels in the plant (e.g., plant and corporate), quality assurance may report directly to the plant manager (e.g., individual performance) and indirectly to corporate management (e.g., product assurance). Any structure must assure checks and balances within the organization to corporate management. These checks and balances must be in place to offset poor priorities and bad decisions that often are driven by poor job descriptions and incentives. Management must recognize the impact of decisions on quality assurance and food safety, both directly and indirectly.
The Solution... should be reflected in job descriptions. Quality assurance and food safety does not happen by accident, it is a result of intelligent effort. It also is dependent on the type of work done throughout other departments within the company. One way to reach all workers with quality assurance standards is through departmental job descriptions. There are various ways to write job descriptions and provide incentives, but creating team incentives from job descriptions is ideal. Performance incentives formed in a way to create teamwork among quality assurance, production, maintenance, accounting, etc. is a beautiful thing to see. Each employee should identify with and strive toward quality assurance and food safety objectives found within their job description and be rewarded with the proper incentives.
The Solution... should be a team effort. It is not enough to hire, train, develop, and retain good employees. For quality assurance and food safety to be truly representative of the culture coming from the board room, cohesiveness must exist among departments and individuals. Quality assurance and food safety communication should be ongoing, along with continuing training and feedback. Promote cohesiveness with quality assurance and food safety committees by evaluating product complaints and sanitation concerns, while working toward continuous improvement. Training employees from other departments and making them cross functional is also a good way to promote cohesiveness. Employees who are more involved help foster a team effort while improving the quality assurance and food safety culture.
Increasing regulations, requirements, and programs is not the right approach to making safe, wholesome products at lower prices. Boardroom leadership, management commitment, organizational checks and balances, well-written job descriptions and incentives, and employee cohesiveness combined make for the best fundamental approach in creating a quality assurance and food safety culture. Integrating a quality assurance-oriented vision, mission, and core values with good leadership, management, and employees is a practical—and sustainable—quality assurance solution for making safe, wholesome products at low prices.
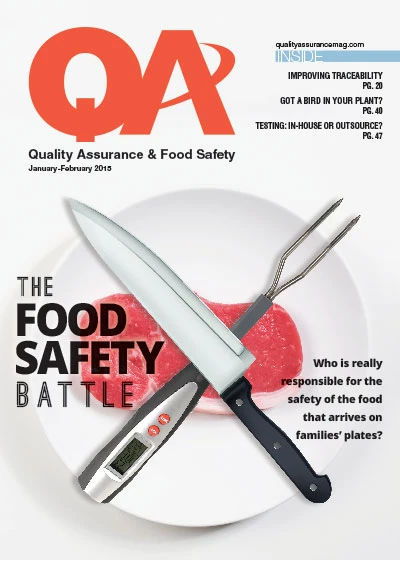
Explore the February 2015 Issue
Check out more from this issue and find your next story to read.
Latest from Quality Assurance & Food Safety
- Q&A: Sandra Eskin Leads Food Safety Advocacy Organization, STOP, as CEO
- STOP CEO Eskin on Government Layoffs, Challenges in Food Safety
- Mission Barns Announces Cell-Cultivated Pork Fat Launch Following FDA Clearance
- Hearthside Food Solutions Recalls Breakfast Sandwiches Due to Undeclared Allergen
- Walker’s Wine Juice Recalls Pumpkin Juice Due to Botulism Risk
- The Cascading Food Safety Impacts of Tariffs on the Food Industry
- Tyson Ventures Calls Startups to Apply for Tyson Demo Day
- Student Finalists Selected for IFT Product Development Competitions