We've all heard the age-old adage "Perception is reality." Whether or not you agree with the concept behind it, it is critical that it be kept front of mind in any plant that deals with live animals.
When the adage was coined, the Internet had not yet been invented, and viral meant the contagion of a sickness, rather than the fast-spreading virility of a tweet, blog, or YouTube video. Regardless of its reality or era, a single undercover video showing what appears to be live cattle on the slaughter line or an employee prodding a pig impacts the entire industry and skews consumer perception of the realities of animal welfare and humane treatment.
![]() |
It is for this very reason that the industry needs to increase its own communication with consumers on its animal welfare practices, procedures, and commitments. In fact, animal welfare expert Temple Grandin believes the industry should be putting out videos of its own.
"The industry doesn't do a good job of communicating with consumers," Grandin said. "We need to be opening up the doors and streaming video to the Internet."
In days of old, people bought their meat from a butcher or raised their own chickens and swine for the dinner table. They knew that their meat came from animals; and to become meat, that animal had to be slaughtered. While the consumer still "knows" this intellectually, many prefer to think of their meat as originating in a neat plastic-wrapped package, rather than from the body of a live animal.
"What's happening is that the public is so far removed, and it is getting further and further removed," Grandin said. "People get so far removed that it becomes shocking."
With this distance comes misperception: That hung cattle is kicking – It's still alive! That employee has a paddle, he is beating those hogs! Without industry communication, consumers don't know that kicking is a spinal reflex, that the waving of plastic paddles or flags is an accepted form of moving pigs.
In-Plant Video In August, the USDA/FSIS released its final Compliance Guidelines for Use of Video or Other Electronic Monitoring or Recording Equipment in Federally Inspected Establishments. The guidance approves the use of video but does not make it mandatory. OSI Industries in Chicago uses remote video auditing (RVA) for internal review of a number of its practices because it provides a unbiased view of performance, said Justin Ransom, AVP of food protection and government affairs. When an auditor is walking around a plant viewing employee practices, the workers see him or her coming and are likely to ensure they are doing the right thing. But when remote video is constantly operating, workers generally revert back to their natural habits—be they bad or good. "RVA is an excellent way to see if your people are really doing what they should be instead of taking shortcuts," Ransom said. "OSI strongly supports the use of RVA in our processes to try to optimize our performance and produce the safest food possible." OSI co-manufactures meat products, so uses suppliers for much of its protein sourcing. It does not require that suppliers use RVA, but it does require that they be audited against the American Meat Institute (AMI) standards for animal welfare. In addition, Ransom said, "we like it when suppliers use it because it is an unbiased audit of performance." OSI encourages its suppliers to implement RVA to improve all its systems, including food safety and animal welfare. "It's a benchmark that they all should consider following," he said. Ransom sees the new FSIS guidance as positive for the industry. "I think it is great that FSIS supports RVA and is encouraging companies to continue using it for improvement." |
"These things need to be more commonplace and ordinary. I think we need to just show it and explain it," Grandin said. "We need to show it to the point where it just becomes ordinary."
Grandin does just that with videos she has posted on YouTube, including "Electric Stunning of Pigs and Sheep,""Animal Care—Taking the Mystery Out of Pork Production," and "Cattle Behavior and Handling."
The videos generate both "likes" and "dislikes" and thousands of comments. While Grandin does remove the filthy "four-letter" comments, she leaves all others, understanding that there will be dissension, but it is the overall communication that is important.
Changing Perceptions. Although it does not use video, Sam Kane Beef Processors in Corpus Christi, Texas, does use the Internet to communicate its animal welfare message, posting an open letter of its commitment on its website. In the letter, the company states:
Sam Kane takes a systematic approach to all humane handling activities and animal welfare issues. … Our company remains committed and will invest whatever resources are necessary, to achieve a safe and wholesome product for our customers.
The management of Sam Kane Beef Processors, Inc. supports and requires the commitment of all our personnel to following the procedures set forth in our programs …
- We will treat animals in our care humanely and with respect.
- We will strictly follow all applicable laws and regulations for animal treatment.
- We will take steps to ensure that our employees and processes meet these standards.
- If we learn that we or any of our employees have failed to follow these procedures, we will take appropriate remedial and disciplinary action.
"Animal handling is a very important component of what we do," said Director of Regulatory Compliance Brian Honigbaum, adding, "We don't do it just because of regulatory, but because it is the right thing to do."
To ensure it continually runs best practices in its plants, Honigbaum said, "We do a hundred-head audit every day, then use that data to further refine the program and identify any potential issues." In addition, the plant follows all AMI guidelines; its cattle pens, restrainer, knocking box, and associated areas were all designed by Grandin to minimize excitement, discomfort, and animal injury; and all employees who have any contact with the animals go through training. "We don't let anyone out there until they have gone through an intensified training program," Honigbaum said.
As the last bullet in the open letter indicates, Sam Kane has a zero-tolerance policy for non-humane handling. Even if an action is a mistake on the part of the employee, the company takes immediate action, providing additional training and giving the employee the opportunity for proper performance.
As such, awareness of how one's actions can be perceived is a large part of employee training and daily action. "Things can be perceived incorrectly, and at any time, someone could be driving by with a camera," he said. "Employees are trained to stop and think, 'What is the perception of what I am doing?'"
Sam Kane does not use RVA in its plants, but Honigbaum understands the importance of keeping up with regulation and current practices and events in the industry. In fact, he said, he has a Twitter feed on his desktop to keep him updated on food safety and recalls, so when a problem arises anywhere in the industry he can be ahead of it. "You have to be a step ahead or you're already a step behind in this industry," he said. As was shown by the Hallmark incident, "if one person makes a mistake, it affects everyone."
While many in the industry may not be quite ready to post video on the web, the more the industry communicates its humane handling practices and educates consumers, the better it will be perceived and the more likely it will be able to change the adage to: Knowledge is Reality.
The author is Editor of QA magazine. She can be reached at llupo@gie.net.
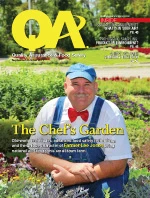
Explore the October 2011 Issue
Check out more from this issue and find your next story to read.
Latest from Quality Assurance & Food Safety
- Catalyst Food Leaders Announces Virtual Leadership Summit for People in Food
- Food Safety Latam Summit 2025 Set for Mexico City
- AFDO Webinar Series Offers Strategies for Difficult Times
- FDA, USDA Rehire Some Staff, Multiple Sources Report
- Nestlé Opens Arizona Beverage Factory and Distribution Center
- Ingredion Invests $100 Million in Indianapolis Plant to Improve Efficiency, Enable Texture Solutions Growth
- Eagle Unveils Redesigned Pipeline X-ray System
- USDA Invests Up To $1 Billion to Combat Avian Flu, Reduce Egg Prices