As shown by the graphic at right, condensed from a real FDA Warning Letter, even bi-weekly pest control service will not keep food safe without the cooperation of the plant staff.
It is exceedingly rare for a non-trapped rodent to actually be sighted during a pest control operator's (PCO) visit, said Daniel Kay, CEO, KRC Industries. In fact, thinking back on all the years he has worked in the industry, Kay could come up with only one or two such situations. Because rodents are nocturnal, they are less likely to be out during a technician's daytime service, and if when they were around, they tend to scatter when the truck pulls in, he said, explaining, "[Sightings] always seems to happen after the PCO has left."
On the other hand, because most plants either operate around the clock or have after-hours sanitation crews, it is very likely that someone in the plant will see a rat or mouse before the infestation builds to the point of the rodent urine stains and excreta pellets noted by the FDA inspectors in this letter, or repeated evidence of activity is logged by the service technician.
Although one's first thought may be to eliminate the implicating log book, its purpose is to provide just such food safety warnings and recommendations—before the FDA does worse. As such, it is critical that plants work with their pest control service providers to keep logbooks updated and to implement and document corrective action.
![]() |
Identification of such sightings, as well as recording of technician service and recommendations, are the very reasons that plants must have logbooks for both, and the reasons that they should be regularly reviewed in PCO/plant management meetings.
In addition, proper maintenance of and attention to the logbooks can help plants during audits and inspections by providing proof that the plant has done everything it needed to for control of pests, said Bobby Corrigan, rodent expert and president of RMC Consulting, Richmond, Ind.
Rodent Logbooks. A former QA manager for Leaf, Inc. and now director of technical services for Rollins, Inc., Greg Baumann has been on both sides of the logbook and sees it as key to integrated pest management (IPM)—whether maintained on paper, electronically, or through the web. By maintaining and reviewing these records, plants and their PCOs can analyze trends to spot areas needing improvement. "Trending is the cornerstone of modern rodent management," Baumann said. "It is the essence of integrated pest management."
The most important reason for maintaining a service logbook is "outright food safety," Corrigan said. "And it is assumed that the logbook will include an activity plot map. That's really important," he said.
When such documentation is maintained, it enables both partners, the PCO and plant management, to sit down and review the logbook and associated map, Corrigan said, adding, "Often when taking the time to do that, you will see that certain exterior bait stations will show more activity than others."
To show how the trending of service logs provides a basis for food safety improvements, Baumann gave the example of a series of visits in which rodent stations were monitored for activity. During the first service visit, bait gnawing was documented in a rodent bait station at the northeast corner; at the second visit, the station in the northeast corner again showed rodent presence; and on the third visit, activity in the same area was again noted.
"This is telling us that there is a trend starting to happen in the northeast corner," Baumann said. Had the activity not been logged each time, the trend may not have been noticed. But with the successive records of similar activity, it became obvious that it was not simply random occurrence, but that further inspection should be conducted to determine the source and cause of the rodent activity.
When documentation shows such trending, the question the QA manager should ask is "Why?" Corrigan said. Are there weeds in the area? Is sanitation an issue? Then answer, what needs to be done to correct the issue?
Sightings Logbook. Similarly, employees are the eyes and ears of the service technician when he is not onsite, Baumann said, and the pest sightings logbook becomes the documentation of that. By reviewing this logbook at each visit, the technician can quickly discern if any area may need further inspection or attention. Comparison of the service and sighting logbooks can provide further analysis, to catch potential problems before they can become adulteration issues.
When reviewing a sightings log, it is also helpful for the technician to be able to see date and time of the sighting, as it enables a review of any extenuating circumstances such as weather, temperature, deliveries, etc., Kay said. This logbook also helps the PCO maintain control, he said. "It helps them go out and set up the job. It gives them a basis for a plan."
In fact, because the logbooks enable such plans, Kay said, if the plant is not providing information to the PCO, "you are wasting a lot of time and money—yours and theirs."
Having been a QA manager, Baumann understands that pests are not always the number one priority on the manager's list of duties. "But," he said, "when you do have a pest problem, it overshadows everything else at that point."
For that reason, Baumann said, it's critical that food plant managers pay attention to the pest control report, and take action to correct structural or sanitation issues, as well as anything that may be conducive to rodent problems.
Such attention to the pest control program can also help keep the technician at his or her best. Even when a plant has a good PCO, a lack of rodent activity or sightings can eventually lead to complacency, Corrigan said. "The technician needs to know that QA is following up," he said, explaining that the QA manager should conduct periodic checks, randomly comparing traps and stations against the entries in the logbook.
When an issue is noted on a service technician's report or through an audit or other inspection, "it's really important to take it seriously," Baumann said, adding, "If something on a report is incorrect, document it; don't just ignore it because that is a liability too."
For example, Baumann once had an inspector comment that a bin in the plant should be painted white. In response to Baumann's query as to where that was specified in a regulation, the inspector responded that it wasn't a regulation, he just thought it'd be a good idea. But because Baumann saw a greater concern with the potential of paint flaking and getting into the food, he declined to follow that recommendation—and he documented exactly that next to the notation.
"If you disagree, document that you are not going to do it and why," he said. "You need to address every issue one way or another."
If pest activity, sightings, and recommendations are recorded but no one is made accountable for analysis and corrective action, the logs can become pointless paperwork—or the basis for a Warning Letter. "You need to analyze the numbers," Corrigan said. "Unless you analyze them, they just stay numbers. They only become data when you do something with them."
Kay agreed that all data and issues need to be reviewed and addressed. "If suggestions get ignored, the situation will get worse, make the PCO's job harder, and increase costs." It also increases the likelihood of adulteration and resulting liability, he said, citing the PCA peanut contamination as an example.
Baumann's final words of advice: "Think like a rodent." If you were a rodent, you would be looking for food, water, and a place to live. "Anytime you can interrupt that by excluding any one of these, you will reduce your chances of an infestation."
The author is Editor of QA magazine. She can be reached at llupo@gie.net.
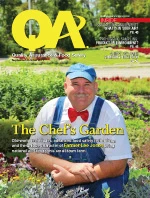
Explore the October 2011 Issue
Check out more from this issue and find your next story to read.
Latest from Quality Assurance & Food Safety
- Catalyst Food Leaders Announces Virtual Leadership Summit for People in Food
- Food Safety Latam Summit 2025 Set for Mexico City
- AFDO Webinar Series Offers Strategies for Difficult Times
- FDA, USDA Rehire Some Staff, Multiple Sources Report
- Nestlé Opens Arizona Beverage Factory and Distribution Center
- Ingredion Invests $100 Million in Indianapolis Plant to Improve Efficiency, Enable Texture Solutions Growth
- Eagle Unveils Redesigned Pipeline X-ray System
- USDA Invests Up To $1 Billion to Combat Avian Flu, Reduce Egg Prices