My 16-year-old daughter, Denae, recently received her driver’s license, enabling her to drive the family car and come and go as she desired—with some parental oversight and limits, of course. One morning, a few weeks after she received her driver’s license, I was preparing to take the car for an important meeting. I settled into the car, reached up and turned the ignition key (that we routinely left in place in the locked garage). Nothing happened. No radio noise blaring through the speakers like when you’re at the front row of an AC/DC concert; no air flow coming through the vents like when you’re sitting near Lake Michigan with the wind in your face; and, most alarming, no engine humming. The cause, as you may have guessed, was a dead battery.
But, what the heck was going on? I started a brief inspection, and quickly found that the key was turned slightly to “On”—which meant that all the accessories had continued to operate through the night, draining the battery. I knew Denae was the last person to use the car, and I told myself to remain calm, because she is a new driver and she did get home safely which is most important for any parent of a teenage driver.
I went back into the house and asked Denae if she recalled turning off the car ignition completely when she got home last night. She said she did, but that after she got in the house, she remembered my standing request to put the electronic car seat back into position number one, so I could get inthe car. You see, my daughter is 5 foot 3 and I am nearly 6 foot 2 with a much larger frame. So when she drives the car, she places the seat as close to the steering wheel and as high as it will go. I, with my long legs and larger body frame, need the seat to be as far back and as low as possible.
But back to the story … When I told Denae that the car key was left in the ignition in the on position, she was extremely apologetic—especially when she recalled that when she went back to the car to reset the seat, she needed to turn on the ignition to do so. She also mentioned that as she was sitting in the driver’s seat as it returned to position #1, she turned off the radio because it was even loud to her in the quiet garage without the engine running. Once the seat was back in “Dad’s” driving position, she got out, and went back in the house. Because the radio was now off, there was nothing to signal her that the car ignition was not switched to off.
Thankfully, in this case, all I had to do to implement a correction and get the car back into operational order was charge the battery. I found our battery charger, hooked it up, and within 10 minutes, the car started, and I was on my way to my meeting with time to spare.
As I drove, I thought about how I had implemented a correction by recharging the battery, but how can we prevent a recurrence? My daughter had fully intended to do the right thing, she just didn’t execute thoroughly to assure the car equipment would function properly the next day. As I drove down the highway, I had an “Aha Moment” of four letters: the four letters that always pop into my head when a negative event occurs: CAPA!
A CAPA Thought.
CAPA is an acronym for Corrective Action/Preventive Action. It is a process to reduce or eliminate recurrence of negative events. In response to an event, a successful CAPA process includes a thorough investigation protocol that drives to root cause. Once this is identified, actions or corrective actions are implemented to reduce or eliminate such events in the future. CAPA can address nearly any event, such as out-of-spec product, complaints, audit observations, and safety events—or even home situations, such as mine
For the CAPA program to be effective, a comprehensive investigation must identify the root cause of the event. Two helpful tools are:
- The Five Whys. When an event happens, ask why it happened; then ask why to that response. Continue to ask why to each subsequent response until the root cause is identified. It may take fewer or more than five whys to get to the root, but the key point is to continue to ask the question until the true source is detected.
- The Fishbone Diagram/Cause and Effect Analysis. The team diagrams the problem as the “head of a fish,” then brainstorms possible causes that affect the problem statement. The factors that potentially contributed to the possible causes are listed as the “fish bones.” Once this is completed, the team selects a few of the possible causes, creates action plans, and analyzes the output toward addressing the problem statement, thus assessing corrective actions and their effectiveness in reducing or eliminating recurrence.
Implementing CAPA.
Back at home that evening … with all five family members around the table, I rehashed the morning’s event and introduced CAPA. I explained that I implemented a correction by recharging the battery, but we needed to address a corrective action and preventive action. Using the “5 Whys,” we determined that if we took the corrective action to remove the key from the ignition and place it on the key ring just inside the house from the garage, we should prevent recurrence of the problem.
As this example shows, the CAPA process can be applied for nearly any improvement activity. At many firms I visit, I see repetitive negative actions such as complaints, out-of-spec conditions, product quality defects, even repeat audit observations. All of these can be eliminated with an effective CAPA program. Some firms say they don’t have the time or personnel resources to implement an effective CAPA program. My response is, “Let’s look at how much time, effort, and energy you are expending to continuously address those repeating negative events.” These firms quickly reconsider after they quantify the resources expended to address their repeating failures.
Take a look at your quality system and the robustness of your CAPA program. If you have a CAPA program and it is effective, I trust that you see the value and the extensive applications where your organization can benefit—even it means taking the car key out of the ignition.
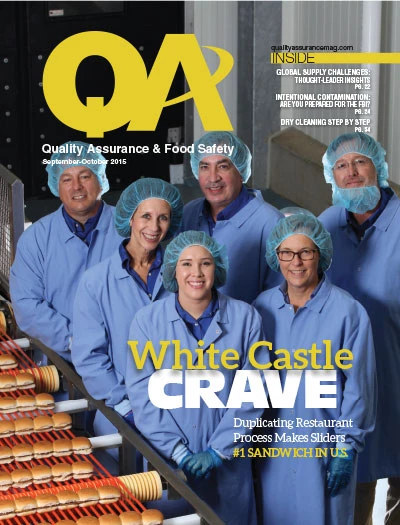
Explore the October 2015 Issue
Check out more from this issue and find your next story to read.
Latest from Quality Assurance & Food Safety
- Joint FAO/WHO Expert Committee on Food Additives Seeks Experts
- FDA Reschedules Webinar on Updated ‘Healthy’ Claim
- Thousands More Laid Off at FDA, CDC in HHS Restructuring
- USDA Extends Deadline on Request for Information for Poultry Quality Standards
- Dessert Holdings Issues Allergy Alert on Undeclared Pecans in Favorite Day Cheesecake
- Idaho Smokehouse Partners Recalls Beef Sticks Due to Possible Foreign Matter Contamination
- IDFA Leadership Symposium Set for June 23-26
- FDA Publishes Searchable Web Page for Food Allergen Labeling Guidance