“The causes of defects lie in worker errors, and defects are the results of neglecting those errors. It follows that mistakes will not turn into defects if worker errors are discovered and eliminated beforehand.” — Shiego Shingo, 1986
Sheiego Shingo, the Japanese industrial engineer credited as one of the world’s leading experts on manufacturing practices and the Toyota Production System, termed pre-mistake discovery and elimination as poka-yoke, which translates to “fool proofing” or more recently “mistake proofing.”
Whether you call it poka-yoke, mistake proofing, or human-error elimination, at McCormick, poka-yoke translates into practice through its Zero Defects/Zero Monitoring program, which includes the installation of vision systems on production lines to eliminate human error in labeling.
Zero Defects/Zero Monitoring is a system designed to “optimize human resources through automated, unassisted, unmonitored zero defects operation,” said Director of Quality Assurance David Mixon. Utilizing a vision system to take over the monitoring for defects means that a technician doesn’t have to stand at the line doing so. Instead, the camera is taught to monitor for defects—with the vision system rejecting or stopping the line if a defect is detected.
“The purpose,” added Corporate Communications Director Jim Lynn, is to “serve the customer to give them the right product with the right label without error.”
Mislabeling. With the process by which labels are printed, cut, and delivered, and the speed at which lines run, the potential for mislabeling exists at any food plant. At McCormick, such mislabeling could result in a consumer opening a bottle, box, or packet to find the package contains basil instead of the labeled cilantro or lemon extract rather than vanilla, causing customer complaints and quality-based product withdrawal.
However, if a mislabeling were to involve an allergen-containing seasoning packet mislabeled as a non-allergenic one, the result could be even more serious, with product recall for undeclared allergens to prevent the potential of allergic reaction in susceptible consumers.
While both mislabeling errors are unwanted, it was undeclared-allergen recall potential that was the primary driver for McCormick’s seeking of a better way. “We wanted to prevent accidental use of labels that did not match the product in the bottle,” Mixon said.
According to the Stericycle Expert Recall Index, which compiles quarterly statistics on recall announcements from FDA, 40 percent of food recalls were due to undeclared allergens or other allergen concerns during the second quarter of 2012, making it the leading cause of recalls and continuing a two-year trend.
Two leading reasons for such mislabeling are error during changeover, and the process by which supplier’s labels are printed and boxed.
Supply Chain Management. Due to the small size of many of McCormick’s labels, its label suppliers print multiple products on a single sheet, then cut them apart. Some of the sheets are cut into single labels and piled. Mistakes can then be made at a number of steps in the production process of cutting, sorting, and boxing of the labels. “If the sheets are mixed, there is no way for a technician on the line to discern three or four wrong labels,” said Jim McKay, McCormick Plant Manager.
For this reason, many of McCormick’s label suppliers have begun adding the systems to their lines as well. Although McCormick does not require this, it is certainly encouraged. “We try to operate on the fit-for-use principle,” Mixon said. “So when an item comes to us, it is fit for use without inspection.”
To further mistake-proof a run, some vision equipment is set up to inspect the labels prior to product fill. For example, dry seasoning packets come in on long rolls, and changeover between seasonings can occur every hour, with 12 changeovers in a single day. Thus, detecting and correcting an issue prior to the packets being filled provides extensive economic gain over attempting to open, empty, and reuse a mix from a filled, mislabeled packet.
To add to the risk, the graphics on the different product packets of this type are similar—and, to the human eye, look virtually the same when the packets zip by at more than 900 per minute. Using a random sampling approach can catch some errors, but it doesn’t necessarily tag a mixed label or an outdated label being placed on a product.
“Inspection is dependent on a lot of things, but it is mainly dependent on people,” said Mixon, who has worked in McCormick’s quality department for 23 years. “The ideal is to get the equipment to do the work for you. As it relates to label inspection, a technician attempting to inspect labels on products zooming down a line is fatigued within 15 minutes. They are just burned out.” Thus, he said, “You want to put equipment on your line that can see better and faster than the human eye.”
So, in 2005, he said, “We started getting serious about vision systems.” Although cameras have been used for a variety of purposes in manufacturing for decades, it was the increasing availability of high-speed cameras, strobe technology, and refinement of 2D coding that enabled the systems to become the primary ingredient of McCormick’s Zero Defects/Zero Monitoring program.
A Process Mindset. It all started when now Vice President of Manufacturing/Distribution Rod Gordon drove the concept at McCormick which reinforced the goal of “making quality once,” that is, right the first time. As a result of increasing complexity in the plants resulting from productivity improvements, human error became more difficult to eliminate. The more the potential of error is reduced, the greater the chance every technician has for success, he said, adding, “If you automate wherever you can, you are freeing them up to succeed.”
Essentially, Gordon explained, “We are taking a process mindset and using it on packaging.” Instead of having to literally see a problem label, technicians now set up, run, and monitor the equipment to do so. “They are responsible for maintaining the equipment, not the process of trying to hand pick a label that has a problem,” he said.
Using the process mindset, McCormick conducted data analysis to determine what problems were causing occasional improper labeling, Mixon said. This included a comprehensive operational review of mislabeling and other failures that caused the company to have to pull together an incident management committee. “If you have executives meeting for one hour, that’s an expense,” he said. The analysis showed that in 2005 and 2006, mislabeling was responsible for more than 50 percent of all incidents.
From that, McCormick conducted a failure mode and effects analysis (FMEA), reviewing each failure to determine the root cause, and assigning a score based on risk and likelihood of failure. For example, the company analyzed how the number of changeovers impacts the number of runs with potential for undeclared ingredients.
Not only did this analysis provide the impetus to begin purchase and installation of the vision systems, it enabled McCormick to set line priorities. “Some lines have a need for a vision system and some do not,” Mixon said. “On the other hand, there are lines that have cameras that can inspect both sides of a package and lines with multiple cameras inspecting for different things. The FMEA process quantifies the risk of something going wrong and the severity of that risk to enable such decision making and prioritization.”
The Vision System. The system works by the fraction-of-a-second shining of a strobe light onto the label as the camera takes a photo of each item that speeds down the line. When McCormick first installed the system, the picture was taken of the UPC code. But because there were some limitations with that, McCormick began moving toward a 2D code, which can be linked to the specific item and changed as needed without having to change the UPC code.
As spices, flavorings, or seasonings speed down the line, the system inspects the label of each. If the 2D code on any label doesn’t match the code the equipment has been programmed to see, it rejects the item. One or two rejections will keep the rest of the products moving, but any more than that will stop the line so the technician can determine the cause and extent of the problem and take corrective action.
“If the vision system is set up correctly and is operating correctly, you have up to 100% rejection,” Mixon said.
Setting the equipment to inspect a 2D code rather than a bar code or other visual on the label has a number of food safety, quality, and even marketing advantages. The 2D code:
- is tiny—as small as 1/8-inch square, so it does not take much room on the label—even when the label is only 1 x 1.25 inches, as are those on McCormick extract bottles.
- can hold a great deal of information, enabling individual tracking and traceability down to the bottle, box, or packet.
- can be changed as often as a product or ingredient change is made, without impacting the UPC code which a retailer must be able to read as well. “If there is a formula change, but a new UPC code is not needed, the 2D code protects us,” said Plant Quality Assurance Manager Kate Cordner.
- does not need to be able to be seen by the human eye. To limit the amount of marketing space taken up by the 2D code, it can be placed in an area that would be covered during the labeling process. For example, if a label fully wraps around a bottle, the 2D can be placed in the overwrap area.
- on McCormick packaging materials is similar to the QR code information that can be read by consumer smartphones. (McCormick has not yet added information for that purpose.)
- is tied into raw material data. If there is a change on the bill of materials, it is coded into the system which ensures that the labels reflect the change. “The dream future is that all your raw materials used to make the product are coded to a particular label, coded to a particular UPC, and coded to a particular bottle or case,” said Vice President of Global Technical Projects Rick Gill. “In the future ideal world, all is linked.”
Quality Control. Although eliminating the possibility of undeclared allergens was the primary impetus behind the installation of vision equipment, the systems have enabled a number of quality controls that have reduced customer and consumer complaints.
In fact, the first systems were installed on the extract line at the Maryland plant because of McCormick’s analysis findings. Each bottle of extract, such as vanilla and lemon, is also packaged in an individual box—both of which are labeled. The possibility existed for the bottled product to not match the box into which it was packed. “We needed to find a way to manage this process,” Mixon said.
The vision system did just that. “Since the system has been installed, we haven’t had a single consumer call about a wrong label,” Cordner said.
As the company continues to bring food safety packaging issues to zero, it is focusing more and more on quality controls, Cordner said. “For example, the auto-detection of case counts, with the vision system rejecting or stopping the line if there are, say, 11 bottles of spice in a 12-count case, is another example of how the system brings poka-yoke into the plant. It makes it ‘fool proof.’ It makes it so a person can’t inadvertently cause or overlook an error.”
Other examples of quality controls for which the system is being used or tested on some lines are ensuring that every bottle is capped, checking for lagging or crooked labels—and rejecting any that aren’t. “We are continually experimenting with various ways to use vision systems to detect quality issues,” Cordner said. “When we have success, we pass it on to other lines and other systems.” The ultimate goal, she said is “making perfect product every time.”
“The process to achieve that,” she said, “is as much a result of technician input as it is of management policy. Our technicians are important in everything we do.” They are involved in the process, bringing ideas from their experience on the floor. “I can’t tell you how many times a technician has come back with an idea that is better than what I would have engineered,” Cordner said, adding that she has often heard a technician say, “I don’t ever want someone to get something from my line that’s not good.”
A Global Standard. Since its first installation of a vision system to match up bottles and boxes, McCormick has installed the equipment on more than 25 lines in its plants, and is now making it a corporate global standard, writing it into the requirements for every operation, Gill said.
The global implementation was not based simply on the accomplishments and standards of a single plant. Rather, Gill said, “the company collected information on all its lines around the world, then conducted risk analyses to determine which would benefit.” From this, McCormick set priorities and mapped out a plan, starting with U.S. plants. With this initiative just about finished, the company is focusing on plants in Europe, and Asia will then follow. “The goal,” Gill said, “is to have completed global implementation in three to four years.
Implementation is not as simple as placing a camera on a line, he added. “You have to first ensure that the camera can ‘talk to’ the system in the plant, and you have to have space for it.” So implementation has also included upgrading many of McCormick’s lines. In fact, the company has experimented with four different vision equipment brands, then narrowed it down to a single brand for most lines. Now when new lines are purchased, vision equipment is a standard specification.
Additionally, Cordner said, “You have to define the standards that are needed for each line.” It can depend on the rate at which a line runs, the lighting that is available (with overhead lighting found to have an unexpected impact on the camera’s ability to see the labels), the need for 360-degree vision, the desire to stop the line or simply reject items, etc. A plant needs to determine what system will work best for the needs of each plant; which will provide the most reliability, she explained.
With the Maryland plant as the pilot test, Gill said, “We proved that the concept works, that this is the right thing for our business. Now we are extending it to the rest of the world.”
Vision systems are not inexpensive, but McCormick has seen the equipment pay for itself in reduced error. Since the company began installation in 2006 through 2012, it spent millions on the systems. However, McCormick believes it has saved hundreds of thousands by eliminating mislabeling incidents.
“If you do it right, you achieve savings,” Mixon said.
The author is Editor of QA magazine. She can be reached at llupo@gie.net.
Photos by Vicki Jeromos Blayney
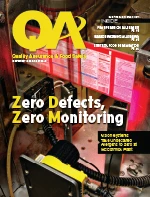
Explore the December 2012 Issue
Check out more from this issue and find your next story to read.
Latest from Quality Assurance & Food Safety
- Bird Flu: What FSQA Professionals Need to Know
- Registration Open for 129th AFDO Annual Educational Conference
- Frank Yiannas, Aquatiq Partner to Expand Global Reach of Food Safety Culture
- World Food Safety Day 2025 Theme: Science in Action
- Ancera Launches Poultry Analytics System
- USDA Terminates Two Longstanding Food Safety Advisory Committees
- Catalyst Food Leaders Announces Virtual Leadership Summit for People in Food
- Food Safety Latam Summit 2025 Set for Mexico City