Question: What do you do when you’ve done all you can to ensure your product leaves your facility pest-free, but your #1 customer complaint is still insects in the food?
Answer: You develop an annual symposium to educate your downstream supply chain on food safety with a key focus on pest infestation—as Purina did in the 1990s.
“We realized years ago that pest infestation was a huge issue with our top brands, and it was not coming out of our factories,” said Nestle Purina Pet Care Director of Retail Food Safety Kim Kemp. The issue was becoming particularly wide-ranging in the 1990s when the big box retailers were shifting from carrying only items such as bikes, clothing, and home goods to stocking half the store with food, he said. A wave of retailers began mimicking that model, but because they didn’t have a background in food handling, most did not have the knowledge to control the pest issues that went along with it.
Additionally, recent decades have seen a progressive shift in pest management, which Kemp describes as “Next Generation Pest Management.” The shift integrates science and strategy rather than relying on traditional, how-we’ve-always-done-it methods; focuses on inspection instead of “ringing the building with rodenticide”; uses data analysis and trending to create the program; and, through all this, serves to increase sustainability and environmentalism.
“Pest management is a science not a cookie-cutter program,” Kemp said, and the facilities need to take as much responsibility for the science- and data-driven programs as do their pest control providers. “It’s not just the pest control industry that needs to change, it’s our managerial approaches to pest control in our buildings that needs to change,” Kemp said, adding, “A lot of the failure of traditional pest control and success of next generation is that people didn’t know there was another option.”
And that is exactly what Kemp and Purina are striving to change; that is, ensuring that their distributors and retailers know the options and have the knowledge to partner with their pest control providers to keep their facilities—and the pet foods—pest free.
A Pest Power Bar.
Although just about any food is attractive to insects or rodents, pet food is particularly susceptible to pests and to consumer complaints, Kemp said. Most of the incoming ingredients are grains and grain byproducts that are very attractive to many insect and rodent pests. “Pet food is like a power bar for insects and rodents,” Kemp said, adding that because of this, “it was very easy for pest control operators to throw up their hands and say it was coming in with the pet food.” Additionally, because dry pet foods are sold in containers as large as 40-pound bags and can be expensive, customers are less likely to simply toss a bag as they might a five-pound bag of flour that had cost only a few dollars.
So Kemp decided to take the initiative to bring Purina pet food distributors and retailers to the manufacturing plant to see Purina’s commitment to food safety and receive training from an array of experts on storage and handling practices for maintaining a quality product. It was the genesis of the Purina Food Safety Symposium and Plant Tour.
Downstream Education.
As explained in the symposium’s accompanying handbook, “The nature of the process for producing pet foods is such that all stages of insects from eggs to adult are destroyed if they would be present in any of the initial ingredients. However, during distribution from production to the final consumer, pests may be attracted to the food.” Thus, both the handbook and the symposium sessions include step-by-step procedures for identifying and correcting problems in the distribution and retail environments.
To develop the educational program, Kemp said, “I used AIB’s model: Bring in the experts and listen to them.” It started small—the first few years were fortunate to draw eight attendees, but after more than 20 years of annual occurrence, the symposium has become so popular that many return year after year, and Purina cannot accommodate all those who ask to participate.
This is because the symposium has proven to be of significant benefit to both Purina and the attendees in education, interaction, and relationship-building. Not only do the participants learn from the session experts, they get a chance to interact with and learn from experts in the non-competitive food safety-focused environment.
The sessions, which include topics from rodent control, next generation pest management, and understanding a pest management provider to future trends in food safety, are focused on practical knowledge and application. The purpose of the symposium is to educate participants to be able to take the knowledge back, apply it in their facilities, and further educate their own employees.
The expertise that is developed is evident in the retailers and distributors who become symposium presenters after attending as participants, working one-on-one with the Purina Pet Care Food Safety Group, and applying lessons learned within their facilities. At this year’s symposium, PetSmart and H-E-B presented their stories.
The PetSmart Story.
In a session entitled, “The PetSmart Story,” PetSmart Director of Contracted Services Mick Moore discussed the pet stores need for and application of preventive measures against pests. “I have to play good defense; I can’t allow these unwanted pests in because I am limited in what I can do if they do get in—because we have live pets.”
Symposium Changes Way Purina Distributors and Retailers Think
|
Like food manufacturing facilities, a critical point of control at PetSmart is the receiving area, with dock doors being a primary entry point for rodents or insects, and no-gap, rodent-proof sealing of critical importance. Moore is currently conducting tests with XCluder products because of their flexibility to fit a variety of gaps and their steel-wool, “Brillo-pad”-like composition that deters rodent gnawing.
PetSmart has also implemented a number of in-store pheromone monitors, harborage elimination techniques, and extensive sanitation practices to manage insects before they can become a problem. And with the chain opening 40 to 70 new stores annually, Moore developed a New Store Inspection Sheet, which includes items such as inspection and sealing of expansion joints, detection of light penetration, etc. “I am not opening any new stores with light penetration coming in,” Moore said.
The H-E-B Grocery Story.
Also speaking was Senior Food Safety Programs Manager Israel Ramos of H-E-B, a large independently owned food retailer based in Texas. Ramos discussed the four “must haves” of pest control, including partnership, program, education, and communication.
- Partnership. When developing a pest control program, managers from each department should be involved along with the internal or external pest control provider, Ramos said. Each can contribute a different expertise; and buy-in, ongoing support, and follow through will be more successful when all are involved in the discussion and understand their roles and responsibilities.
- The Program. It is important to develop pest control as a cohesive program—much as you would a HACCP plan. Your pest control should not be an unorganized or as-needed effort. Additionally, the program should be reviewed and updated regularly.
- Education. The program should include development of a training program as well as designation of trainer(s), trainees, and topics. On what does each group of workers need to be trained, and what is the best method for each?
- Communication. Initial and ongoing communication between departments, the pest control operator, and employees is critical to ensure all aspects of the program are correctly implemented. Otherwise, Ramos said, there will be a lot of “finger pointing.”
H-E-B has retail, warehouse, and manufacturing facilities, and the program is customized to each, with retail being primarily inspection driven, and warehousing and manufacturing focused on strategically meeting audit and inspection criteria, such as SQF and HACCP, along with regular inspection of all food and non-food areas.
“It is a new way of thinking,” Ramos said. One that is data driven, and logic driven if no data exists.
Upstream Education.
It is not only the retailers and distributors who learn from and network with each other at the symposium, rather the event provides Purina with the opportunity to learn from its downstream supply chain, continuously build on its relationships, and develop and conduct trials in various facilities to further improve programs at all levels.
- Rodents. One of the most extensive programs was the 2 1/2-year field study conducted with Walmart and Purdue University to determine the efficacy of standard pest programs and whether rodenticide use could be reduced. The research found that the rodent programs in the studies could be more “green” (i.e., rodenticide reduced), but even more surprising was the finding that the number of rodents traps ringing facilities could be reduced—often by as much as 60%, without impacting rodent catch—providing more time for inspection and interior control. (See Next-Generation Rodent Management Moves Off the Wall by Kim Kemp, QA March/April, 2013.)
Although the field studies have proven the method to be effective, it is not always an easy sell, even at Purina. “I was not a big proponent when it started,” said Denver QA Team Leader of Quality Systems Ben Gurski. “I was scared. I didn’t want to give up traps; I thought they gave me control. I had a hard time letting it go, but it wasn’t so hard at the end when I realized it worked.”
The plant reduced its rodenticide use by 70 pounds a year, and saved 17 hours a month by reducing trap numbers. “What do we do with those 17 hours? That’s the important part,” Gurski said. In Denver the time is spent inspecting incoming materials, outbound shipments, educating employees, ensuring proper rotation, conducting monthly audits —and checking equipment placed near plant entrances, then following up on any activity. “Our expectation is to never see any activity in any of our traps, but how realistic is that?” he said. So follow up is conducted to determine root cause and take corrective action.
- Stored Product Pests. Indian meal moths, grain beetles, and weevils are all major issues for pet food manufacturers, distributors, and retailers. As such, Purina Program Manager, Retail Food Safety North America and Latin America Stefan Goodis has been conducting a trial in various retail operations on a mating disruption control system for Indian meal moths. For analysis, traps have been set in 31 pet specialty stores in five states and five grocery stores in two states from which data has been collected over a two-year period. While no single technique is foolproof, it has been found that, Goodis said, “This is as close as we will ever get to a silver bullet.”
To date, the traps have caught over 44,550 Indian meal moths. Correctly installed traps can reduce the moth activity by 93%, he said. Even when installation was not completely correct in the test (to allow for human error), a 75% drop was seen; and when the traps were installed at less than the labeled rate, there was still a 25% to 51% reduction in moth activity. However, Goodis cautioned attendees that trapping must be combined with proper sanitation and product-handling practices to be effective. “It’s a tool you can use that is very effective providing you’re doing everything else and other steps have not been enough to get you over the hurdle,” he said.
Purina also currently works with PetSmart on other options for replacing the tape seal of dry pet food bags with a glue seal, and it focuses strongly on forecasting of product sales to more closely align stock amounts with sale to reduce time on shelves—thus reducing potential for pest infestation.
In the Plant.
In addition to two days of presentations, symposium participants have the opportunity to tour Purina’s manufacturing plant, with stops at various points in the process where facility workers introduce themselves, detail plant practices, and respond to questions.
The Denver plant that was visited has been in operation since 1930, having begun as a producer of livestock feed, converting to Purina Dog Chow in 1958, and today producing a variety of Purina dry dog and cat food. The involvement of the workers in the tour presentation is evidence of its standard practice of employee empowerment, where food safety and quality are everyone’s responsibility, said Assistant QA Manager Andrea Laake. “We talk about food safety a lot. If [a worker] notices something wrong, it is their responsibility to shut down the line and let someone know.”
Much of the plant’s system is automated into as few steps as possible. “The less you handle a product the better it will look when it gets to the customer,” said Denver Forklift Operator Tom Pierce.
Responding to a question on how much the plant cleaned up for the visit, Pierce responded, “It always looks like this; we take pride in it.” Just as it is every worker’s responsibility to shut down a line if there is a problem, it also is every worker’s responsibility to clean up a spill, damage, etc. as soon as it happens or is seen. “We constantly clean as we go.” In fact, he said, the plant has an open-door policy. “You can call today and say you want to come in tomorrow, and usually you can do it,” Pierce said.
Results.
It is difficult to measure the value of the symposium to Purina by any specific figures, except to say that infestation is no longer its #1 customer complaint … and Purina’s efforts have positively impacted the supply chain of competitive pet foods as well.
When Purina was purchased by Nestle in 2001, Kemp was unsure if the company would continue to fund the annual symposium. So he asked the question of his new supervisor, previously with Alpo (also a Nestle brand), who responded that they had no intention of discontinuing the program. While he was at Alpo, he said, “We knew what Purina was doing because our complaints went down too.”
“It’s all about brand protection,” Kemp said. “A lot of problems are laid at our doorstep when distributors, retailers, or their pest control companies don’t have the skills to control them.” Thus, as Kemp said to participants in the opening session, “The purpose of the symposium is for you to take the knowledge home and become the experts.”
The author is Editor of QA magazine. She can be reached at llupo@gie.net.
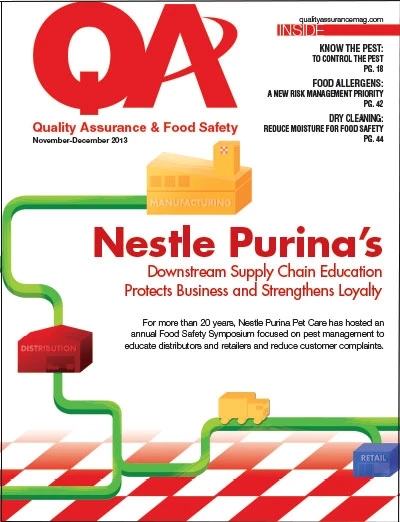
Explore the December 2013 Issue
Check out more from this issue and find your next story to read.
Latest from Quality Assurance & Food Safety
- Bird Flu: What FSQA Professionals Need to Know
- Registration Open for 129th AFDO Annual Educational Conference
- Frank Yiannas, Aquatiq Partner to Expand Global Reach of Food Safety Culture
- World Food Safety Day 2025 Theme: Science in Action
- Ancera Launches Poultry Analytics System
- USDA Terminates Two Longstanding Food Safety Advisory Committees
- Catalyst Food Leaders Announces Virtual Leadership Summit for People in Food
- Food Safety Latam Summit 2025 Set for Mexico City