
By Lisa Lupo
In 1906, President Theodore Roosevelt signed into law the Food and Drug Act, specifying, for the first time, that it shall be unlawful for any person to manufacture, sell, or transport any adulterated food, with the definition of adulterated including any food that “consists in whole or in part of a filthy, decomposed, or putrid animal or vegetable substance, or any portion of an animal unfit for food.”
Although pests have fallen within this definition of adulterants since then, it is only with the passage of the Food Safety Modernization Act (FSMA) that GMPs — including those for pest control — transitioned from guidance to regulation, and that pests were specifically named as one of the hazards requiring preventive controls and inclusion in a written Food Safety Plan. That conversion to law has brought with it an even greater focus on pest management standards and innovative technologies for food facilities.
INTEGRATING TECHNOLOGY. To meet, or exceed, today’s requirements and standards, food facilities need to ensure that the pest management service provider they select is truly capable of solving any common pest problem that poses a threat to its brand, said Chris McCloud, McCloud Services president and CEO and author of the white paper What You Should Expect from Your Pest Management Professional…What They Should Expect from You. Thus, in addition to controlling pests, pest management professionals (PMPs) should have the technologies that enable them to analyze and interpret quantitative and qualitative data.

“PMPs don’t necessarily need to be at the cutting edge of technology, but they cannot be at the handle either,” McCloud said. That is, they should have access to advanced technology which provides electronic data collection and the ability to conduct predictive analysis. The benefits of these include:
- Consistency and Accuracy of Information. Especially for those who operate multiple locations, technology can enable you to have site information delivered consistently, accurately, and in a timely manner — for all sites.
- Time Savings. Technology can improve your audit preparation by enabling you to capture information and access it whenever you need it. Because you have access to the information at a key stroke, the time required to prepare is significantly reduced.
- Increased Success of the Pest Management Program. Site data can be used for trending of pest pressures and developing practical threshold action plans. Threshold action plans support a solution-oriented integrated pest management program, McCloud said, and trending supports strategic placement of equipment and use of pesticides and provides a more efficient program.
These benefits also help companies comply with FSMA’s Preventive Controls rule. While the rule states that records (except the food safety plan) may be stored offsite, they must be able to be made available to FDA within 24 hours of request for official review. Supporting the use of technology, FDA adds, “The rule allows for use of any available information technology (e.g., in the creation and retention of records) that will allow industry to comply with the rule, and we encourage the use of information technology to streamline compliance.”
ELECTRIC MONITORING. One of the newest technologies that aids in FSMA compliance and provides many of the benefits are 24/7 remote electronic monitoring systems for rodent control stations. “The box is doing a job for you all the time, so it needs to have more than an alert,” said VM Products President Ethan Vickery.
As such, electronic monitoring which includes a software program integrated with a sensor, provides value in its active, real-time data collection. “The hardware gives the alert, the software gives the data; and it’s important that the elements talk to each other,” said IoT Box Systems Vice President of Business Development Ronen Amichai, with whom VM Products developed its electronic rodent monitoring bait stations. That is, the delivery of real-time data of rodent entry into a station enables you to track and trend each unit and use this information in ways that were not previously possible, Vickery said. For example, you may see that a station just inside the dock door is capturing rodents every Monday afternoon … the same day and time as your regular deliveries from XYZ supplier. This gives you a strong indication that the rodents are coming in with the delivery, the doors are being left open at this time, etc. It provides a starting point for further inspection.

Because the system is active, not passive, “you get dynamic information, so you can make dynamic decisions,” Vickery added. This means, however, that a person must be responsible for paying attention to it, then be ready to act to inspect for root cause and take corrective action, whether that is performing exclusion work or simply reminding employees to not prop open doors.
“The longer the system is in place, the more meaningful the data becomes,” Amichai added. In addition to measuring trends, “you can understand why things happen, because it is also gathering data from the human side — the pest management professional’s reports.” Then, from this, they can redirect their time to the hot spots.
“In the past, everything was static, but electronic rodent monitoring is a dynamic net that takes it to a whole different level,” Amichai said, adding that FSMA is taking the whole concept of the value of a food company to a higher level. “Electronic rodent monitoring gives you several pieces of what FSMA requires on a real-time basis.”
A NEW STANDARD. Electronic monitoring has, in fact, become important enough in the food industry that the National Pest Management Association (NPMA) added a section on the topic to its recently revised 2016 Pest Management Standards for Food Processing & Handling Facilities (previously titled Pest Management Standards for Food Plants, last revised in 2013).
As the Standards state, “Remote electronic monitoring technology for pest management devices provide an opportunity to use advancements in technology to improve the overall efficiency and effectiveness of pest management activities.” NPMA, it adds, “views this technology as a viable addition to a sound science-based IPM strategy.” But, said NPMA Director of Public Policy Andrew Bray, you also need to have data that backs up the fact that the technology is working.
While sanctioning the technology, the 2016 Standards took a step back in recommendations on spacing of rodent stations. In the 2013 Standards, Bray said, “Rodent monitoring moved away from prescriptive.” Instead of specifying exact measurements between stations in conformance with some third-party audits, the 2013 Standards supported placement “based on rodent pressure determined by infestation potential and history rather than predetermined, arbitrary placement without justification.”
However, it was found that, at food facilities that did not have historical data of rodent catch, technicians were having difficulty determining where stations should be placed. Thus, the 2016 Standards recommend that placement be based on history, but add a distance option: “If the previous 12 months of historical data is unavailable, or changing conditions make it difficult to determine the exterior rodent pressure at the time of the assessment, it is suggested an initial spacing placement of 50 to 100 feet.”
Another important section added to the 2016 Standards is a sample risk assessment, Bray said. Including a scoring key, it fulfills the FSMA requirement for risk assessment of pests. In fact, a primary purpose of the issuance of new Standards was to provide updates and improvements to better address changing regulatory requirements, new technologies, and better IPM practices.
While the Standards are intended as general guidance “and require the use of independent judgment when implementing a pest management plan,” NPMA’s goal is to have the Standards become the standard for the industry, Bray said. Thus, the 2016 version been written to meet and exceed requirements of GFSI as well as FSMA. So, if a facility is following the guidance in the Pest Management Standards for Food Processing & Handling Facilities, it can feel assured that it likely will meet or exceed audit standards as well. (The Standards are available from the NPMA online store.)
The author is editor of QA magazine. She can be reached at llupo@gie.net.
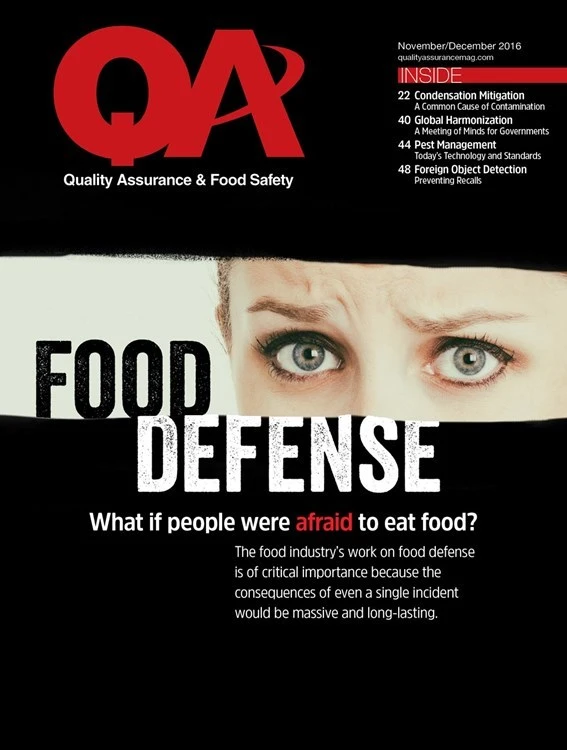
Explore the December 2016 Issue
Check out more from this issue and find your next story to read.
Latest from Quality Assurance & Food Safety
- AFDO Webinar Series Offers Strategies for Difficult Times
- FDA, USDA Rehire Some Staff, Multiple Sources Report
- Nestlé Opens Arizona Beverage Factory and Distribution Center
- Ingredion Invests $100 Million in Indianapolis Plant to Improve Efficiency, Enable Texture Solutions Growth
- Eagle Unveils Redesigned Pipeline X-ray System
- USDA Invests Up To $1 Billion to Combat Avian Flu, Reduce Egg Prices
- Washington Cats Confirmed with HPAI as Investigation into Contaminated Pet Food Continues
- USDA Confirms Bird Flu Detected in Rats in Riverside