
A trailer packed with pallets of product pulled into Kessler’s Food Services in Camp Hill, Pa., and with an inspection checklist in hand, a receiving team conducted the multipoint audit — a required precursor to welcoming any supplies or materials into the loading dock.
“The one trailer that came in, we could see that it was not very clean,” said Quality Assurance Director Amela Romanic. “There was loose dirt, almost like they had been delivering garden items first. We said, ‘Sorry, we cannot accept this product with the trailer in that condition,’ and the driver had to take it back.”
A concerted effort at Kessler’s Food Services to provide tools and education so employees keep a trained eye on the facility for pests informs thorough company-wide protocols.
Small group training occurs monthly and includes walking the facility to point out areas to watch. A log is available to record sightings. In-house inspections are combined with those performed by a pest management provider. Even basics like keeping doors closed are regular reminders.
Employee education is a critical component to control. More eyes mean less room for error.
“We are very strict about our house rules,” said Chris Dodson, QA manager and SQF practitioner at Atkinson Candy Company in Lufkin, Texas.
Atkinson Candy also maintains a sightings log, and Dodson emphasizes the importance of including specifics. “I’ve been drilling the team with the need for details,” she said. “Don’t just write [down that] you saw signs of a pest in the kitchen, which is 50-by-40 feet and has an upstairs. Say, ‘I saw it in the caramel kitchen by the third cooker against the wall.’”
The 1957-built facility in east Texas is located close to a wooded area and creek. “We have sweet stuff, so [rodents] like to come and visit,” she said. “But we have not had one inside.”
Since joining the company in November 2023, Dodson has only spotted one rodent outdoors. “It participated in the treatment in the bait and laid down and died outside of the box,” she said.
Dodson has been in the food processing industry for 49 years and recognizes that rodent monitoring and best practices require a multi-pronged approach and all-in attitude.
“Employee engagement is key,” she said. “See something, say something.”

LAYERS OF OPPORTUNITY.
Understanding the mechanics of a facility is the key to effective monitoring and control, said John Harvey, commercial sales division manager at Truly Nolen, where he serves large-scale food and beverage accounts.
From environmental impacts to a facility’s structure, initial assessment visits begin with a walking tour to identify potential points that could introduce a rodent problem. Receiving areas with rollup doors, food storage spaces, trash receptacles, break rooms — these are some hot spots Harvey identified.
“Dumpsters are a big, conducive area for rodent activity,” he said, noting that Truly Nolen works with facilities’ sanitation partners to ensure proper bin positioning to reduce the potential for rodent activity. “If there is a dumpster corral 25 feet from the building, let’s get that across the parking lot, and then we make recommendations in terms of treating the dumpster.”
Bobby Corrigan said weekly “pilot’s walks” through key areas of a facility are essential. “You can’t say, ‘I’m busy.’ Everyone is busy, and with that attitude of, ‘I have a person who takes care of this,’ that is where situations go south,” said the owner of RMC Pest Management Consulting in Briarcliff Manor, N.Y. “There is no shortage of really effective tools when used correctly, but nothing beats preventive inspections.”
COVERING ALL THE BASES.
Harvey agreed, “We have more at our disposal now than historically to combat the problems.”
He cites an uptick in repellents that when married to a traditional program with traps and bait stations can prevent rodent entry. Namely, an exterior liquid repellent barrier treatment offers a layer of protection in conjunction with bait stations, strategically placed every 50 feet along a building’s exterior, especially in high-density areas like receiving zones.
“In conjunction with that, we include an interior program with mechanical traps on either side of all doorways,” Harvey said, noting that rodents like to run along walls “because they feel safe.”
Truly Nolen offers its commercial customers a program that includes rodent bait stations with Bluetooth capabilities. The system links to its customer portal, providing complete transparency, Harvey said.
“We set up the remote stations around the property in zones, and when technicians arrive, they activate the Bluetooth and can see any activity that occurred in those bait stations,” Harvey said. “This helps with our response time, and when we give that feedback to clients, we can provide real-time data points and identify areas where we need to bolster our resolve.”
While 52% of QA rodent survey respondents said they are familiar with remote monitoring, just 20% of participants reported implementing electronic monitoring. Most said the reason for not using it is because their current rodent control measures are sufficient, and 39% said their pest management provider did not suggest this solution.
Ultimately, remote monitors are the canary in the coal mine, Corrigan said. “You need both,” he said of pairing remote monitoring with human intervention.
Electronic devices do not stand alone effectively.
Remote monitoring can inform a collaborative pest program, but Corrigan said the technology hasn’t taken off like he expected when it came on the scene. “I was the first scientist on board to say, ‘This is a game change for our industry,’ but that has not really happened,” he said, citing cost as one barrier.
Rentokil Technical Service Director Pat Hottel agrees that remote monitoring did not spread like she initially predicted. “That doesn’t mean it won’t,” she said, adding that there is opportunity as facilities increasingly adopt automation and robotic lines where technicians cannot easily inspect due to safety concerns.
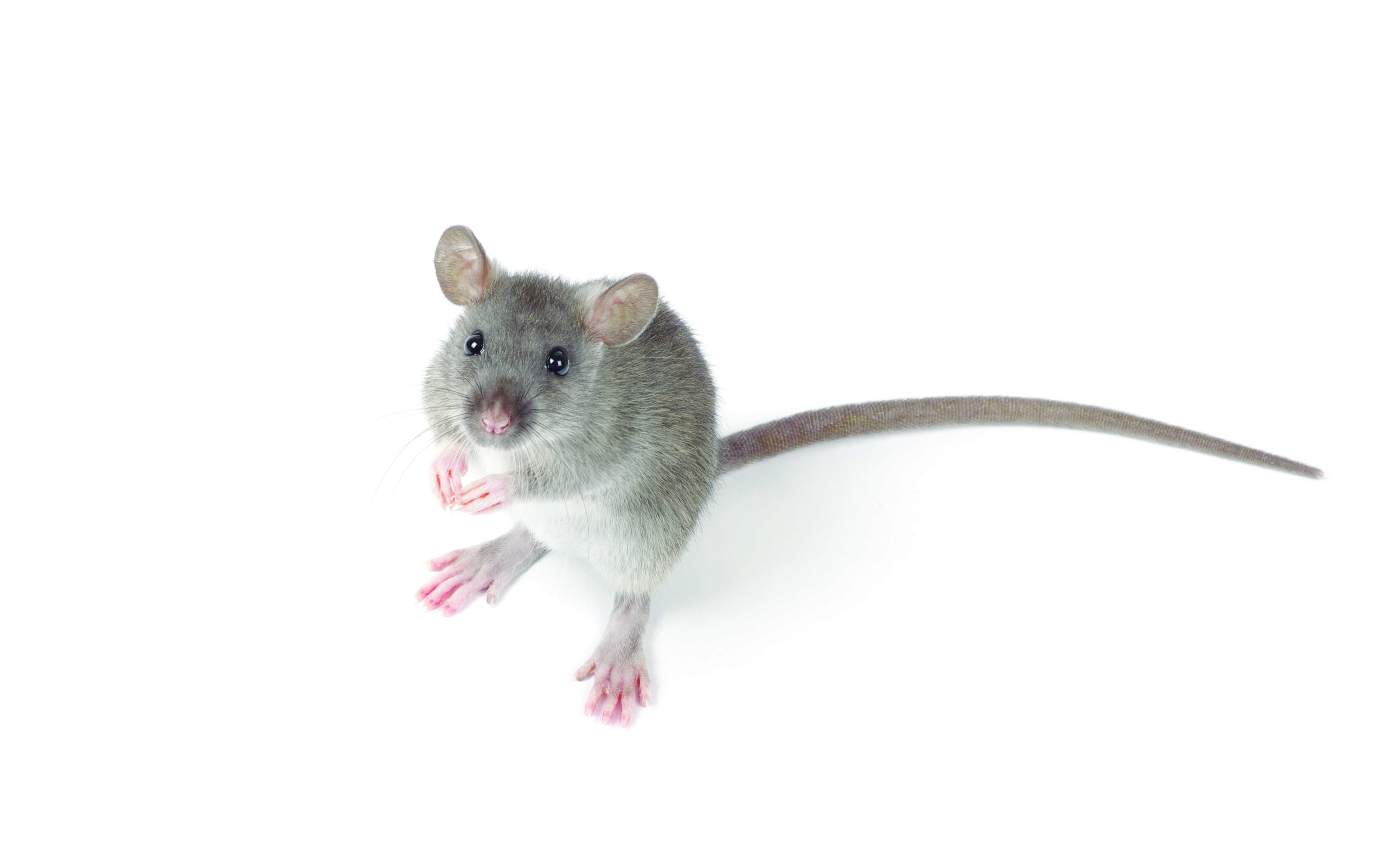
EXCLUSION, INCLUSION & MORE.
Hottel also emphasizes exclusion as imperative to a facility’s pest management program. This includes checking door seals and any gaps that are a welcome sign for rodents.
Additionally, fumigation is another preventive measure against rodent entry and presence in a food facility, according to 7% of survey respondents. In fact, 20% of those surveyed said fumigation options have been implemented at their facilities.
Dodson said a logbook helps inform repairs, as well. “Rodents can go up through pipes and they are very good at finding areas around insulation, so we watch those carefully,” she said, noting that their facility includes a connected pipe that runs across the parking lot to where sugar and corn syrup is stored. “We make sure that is very well sealed so there is no place for any ‘friends’ to come in.”
All this circles back to training, and facilities can work with their pest management professionals to deliver education to employees. “We offer semi-annual pest identification and sanitation training where we talk about how to create a better environment,” Harvey said, noting that these sessions go over regular walkthroughs and pest management recommendations to help create a culture of awareness.
“The key to prevention is good standard operating procedures (SOPs) so staff is well aware of how to prevent rodents or report a concern,” he said.

Explore the July/August 2024 Issue
Check out more from this issue and find your next story to read.
Latest from Quality Assurance & Food Safety
- Hearthside Food Solutions Recalls Breakfast Sandwiches Due to Undeclared Allergen
- Walker’s Wine Juice Recalls Pumpkin Juice Due to Botulism Risk
- The Cascading Food Safety Impacts of Tariffs on the Food Industry
- Tyson Ventures Calls Startups to Apply for Tyson Demo Day
- Student Finalists Selected for IFT Product Development Competitions
- Martin A. Makary Sworn in as FDA Commissioner
- Cargill Kitchen Solutions Recalls Liquid Egg Products Due to Unapproved Substance
- Eagle Product Inspection’s PXT and SimulTask PRO Integrate for Contaminant Detection