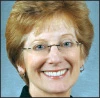
Sanitation used to be called "housekeeping," a term many experienced pest management professionals (PMPs) still prefer because it implies reducing clutter; picking up messes; sweeping, cleaning, and polishing surfaces; and keeping everything in good repair.
We've all seen homes that could have been models for Good Housekeeping magazine. We've also seen homes where "housekeeping" meant something much different. Then there's the occasional news story about a home so cluttered you couldn't walk, that was horribly infested by cockroaches, rodents, and other pests. Just as people's definitions of a clean house vary, employees at food plants, including sanitarians, often do not share a common view of sanitation or good housekeeping.
What's being communicated in your facility when you say to an employee, "Clean it"?
What is "Clean"? You might discover an area that looked clean, but had trash hidden out of sight. Or, sometimes a problem isn't deliberately hidden. For example, almost all maintenance personnel can tell unbelievable stories about what they have found inside a void (e.g., a wall), when working on repairs. In the Midwest, siding installers talk about finding the space beneath old siding packed with dead boxelder bugs . . . and live warehouse beetles. It's surprising; but no more surprising than to hear occupants say, "I had no idea they [the pests] were in there."
There's no question that sanitation affects pest management. It's not a guarantee that a great sanitation (housekeeping) program will prevent all pest problems. However, a poor sanitation program always increases the risk of major and expensive pest issues.
Integrated pest management (IPM) needs to be part of the daily culture at your facility. Beyond sanitation, IPM demands conducting thorough inspections that focus on exclusion, quality, and mechanical control, as well as physical or structural control.
Simple Structural Improvements. Imagine the huge number of critters that can enter a facility during a single warm night. Repairs and sealing of openings should be done immediately. It doesn't cost any more to fix something right away than a few weeks later. Delays in simple repairs (e.g. closing a gap underneath a door) can become very expensive and include customer claims, regulatory actions, and loss of business, in addition to the cost of solving a pest problem that could easily have been prevented.
Further complicating maintenance of structural integrity, recent changes in rodenticide label wording requirements are critical to understand and discuss with your PMP. On June 4, the EPA passed a new Rodenticide Risk Mitigation Decision for 10 rodenticides (www.epa.gov/oppsrrd1/reregistration/rodenticides/finalriskdecision.htm) to mitigate associated risks to non-target animals such as "non-threatening rodents and their predators" and exposure to children. New labels limit rodenticide placement to within 50 feet of buildings.
This change will impact rodent prevention inside your facility, as well as how to deal with garbage, storage facilities, and other equipment and facilities not part of or attached to food processing buildings. Rodents may travel as far as 500 feet to seek food or when dispersing, but 50 feet is only about the length of the space of a tractor/trailer rig while it's unloading at your dock door, creating the potential for a greater number of rodents closer to your building. No facility can let a rodent problem become established in food areas. So, what can be done to mitigate these changes to your defensive perimeter?
Your remaining lines of defense need to be strengthened such as:
- Add more rodenticide and trap stations near plant openings (e.g., doors).
- Add rodent devices on the interior, especially near doors and outside openings.
- Monitor the interior more thoroughly and more frequently to detect pest incursions more quickly.
- Inspect the entire facility on a planned rotation basis so all areas are thoroughly assessed every few months. While looking for evidence of rodent presence, include places that are usually overlooked (e.g. voids, non-food areas, employee desks and lockers, etc.).
Don't forget to concentrate on structural repairs to build your defensive perimeter. Keeping rodents outside your building is the goal—so caulk, seal and repair gaps, cracks and crevices. Look for holes and gaps in screens, door sweeps and thresholds, drop-ceilings, and dock plates—and fix them!
Outside, remove weeds, brush, and bushes that provide rodent harborage. Consider placing a foot-wide gravel perimeter around your building with rodent devices.
And, clean, clean, clean. Remove food and water sources for rodents both inside and outside buildings.
Remember, it's illegal to apply a rodenticide in a manner inconsistent with the label. So, in consideration of the changes to rodenticide labeling, you need to evaluate your rodent management program and protocols. Keep in mind the following key questions:
- Will rodenticide label changes impact my program?
- Will increased rodent pressure from outdoors increase contamination issues in food areas of my facility?
- Although trapping is the first choice indoors, when would I consider or allow the use of a rodenticide indoors? What if 20 mice were trapped in one week? What if there were fresh rodent droppings every morning but none were being trapped?
And, be careful of saying "that could never happen here." Some incredible rodent problems have ruined unprepared facilities. You can learn from their bad experiences and avoid becoming the example yourself.
Deni Naumann is President of Copesan Services and a member of the National Pest Management Association (NPMA) Bed Bug Work Group.
Latest from Quality Assurance & Food Safety
- Nestlé Opens Arizona Beverage Factory and Distribution Center
- Ingredion Invests $100 Million in Indianapolis Plant to Improve Efficiency, Enable Texture Solutions Growth
- Eagle Unveils Redesigned Pipeline X-ray System
- USDA Invests Up To $1 Billion to Combat Avian Flu, Reduce Egg Prices
- Washington Cats Confirmed with HPAI as Investigation into Contaminated Pet Food Continues
- USDA Confirms Bird Flu Detected in Rats in Riverside
- Kyle Diamantas Named FDA’s Acting Deputy Commissioner for Human Foods
- QA Exclusive: Food Safety Leaders React to Jim Jones’ Departure, FDA Layoffs