
An effective Employee Hygiene Program is a critical component in the prevention of production zone contamination, and sanitizing shoes and boots before entering “clean zones” is imperative. Even the most stringent hand hygiene and gowning protocols can be completely compromised when there is ineffective footwear hygiene. Meritech President Michele Colbert explains the importance of fully automated systems for hand hygiene and footwear sanitizing to prevent the entry of pathogens into production areas.
1. How can footwear sanitizing practices damage employee hygiene SOPs and create contamination risk?
The reality is that some standard industry practices have been proven to be ineffective and can result in the spread rather than the elimination of pathogens from footwear. For example, manual footwear sanitizing pans, door foamers, dry quat pellets, or pails with brushes for manual scrubbing of shoes are potentially, and in fact usually, ineffective. Any employee hygiene practice that allows for variability or that requires manual intervention will be inconsistent and create contamination risk.
2. What is the key to an effective Footwear Hygiene Program?
The key to effective footwear sanitizing and hygiene is having the ability to validate effectiveness consistently. To be effective, footwear sanitizing needs the appropriate “kill” concentration of sanitizing chemical and the appropriate “contact time” required for the chemical to be effective. Traditional footwear sanitizing options can lead to risks in these areas including variability in chemical concentration over the floor or minimal contact time on each foot. Food production companies need to test and validate both concentration and contact time for footwear process effectiveness.
3. What are some of the questions to ask when evaluating a captive footwear program?
Captive footwear and controlled sanitizing SOPs for captive footwear are clearly on the way to becoming a mandatory food safety requirement in the U.S. There are many factors to evaluate, but the most important is to ensure consistent validation of effective sanitizing SOPs. Additional factors to evaluate are space considerations, traffic flow and zoning, cost, and footwear and tread pattern selection for overall cleanability, comfort, and safety. Our HACCP certified team can help consult on an effective program.
4. What makes Meritech Handwashing and Footwear Sanitizing different and more effective?
All of Meritech’s equipment is fully automated, requiring no manual intervention and eliminating variability. Meritech Handwashing Systems are clinically proven to remove 99.98% of pathogens from hands and seamlessly integrate with fully automated footwear sanitizing pans or boot scrubbers that automatically maintain required PPM levels of sanitizing chemical and increase contact time to eliminate footwear as a vector for the spread of pathogens. We just introduced our newest footwear sanitizing product, the Sole-Clean Dry Step, for use in dry and semi-dry production zones.
5. Why use Meritech as your Employee Hygiene partner?
Our complete line of footwear scrubbing and sanitizing equipment, like our handwashing systems, is manufactured in the U.S. and has an industry best five-year warranty. Our equipment is easy to clean and maintain, and the proper “kill” level of chemical is guaranteed as our machines are professionally calibrated, certified, and supported by our team of Service Engineers. Our team of industry experts is here to support and achieve employee hygiene and food safety excellence.
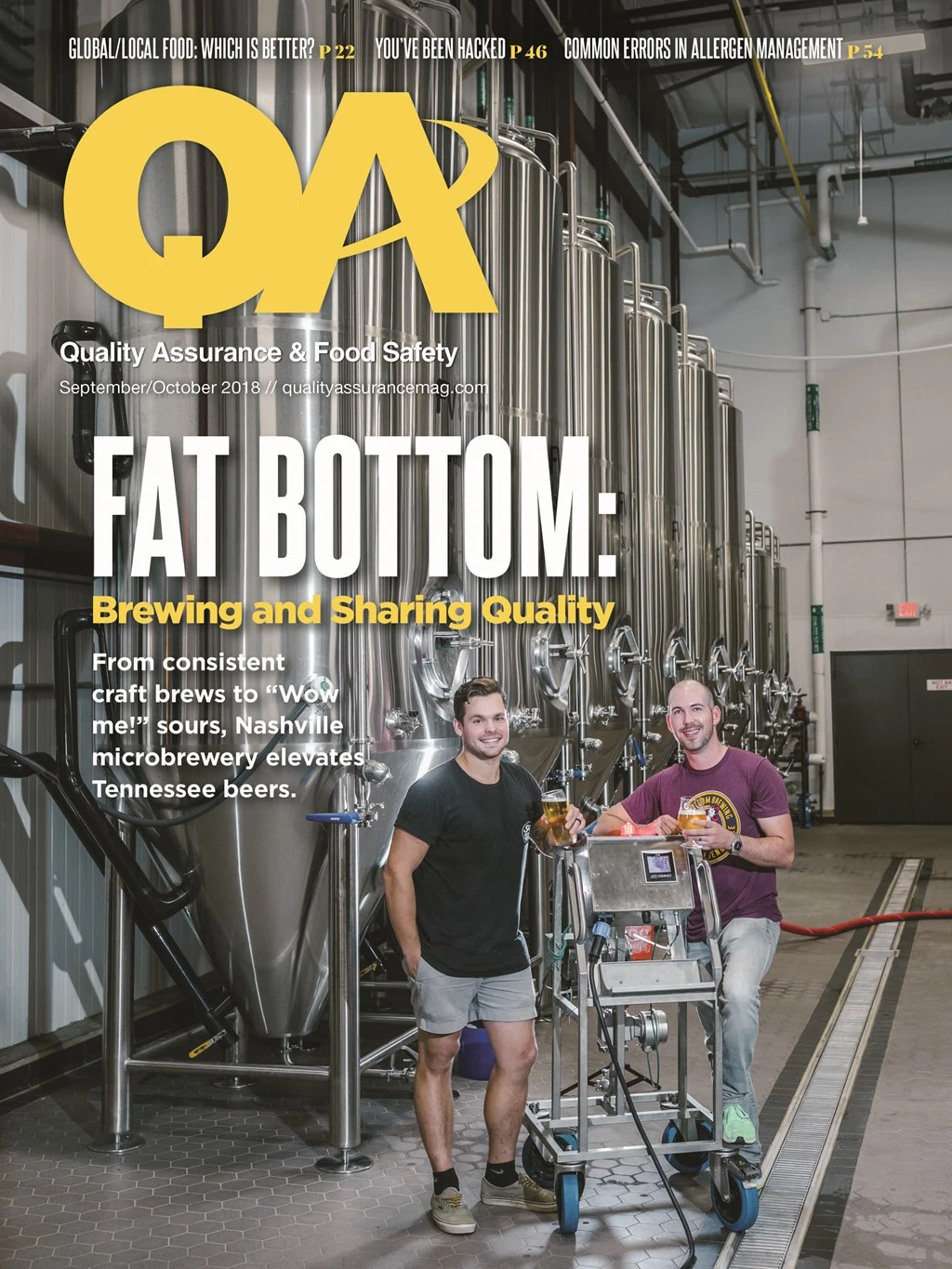
Explore the October 2018 Issue
Check out more from this issue and find your next story to read.
Latest from Quality Assurance & Food Safety
- Bird Flu: What FSQA Professionals Need to Know
- Registration Open for 129th AFDO Annual Educational Conference
- Frank Yiannas, Aquatiq Partner to Expand Global Reach of Food Safety Culture
- World Food Safety Day 2025 Theme: Science in Action
- Ancera Launches Poultry Analytics System
- USDA Terminates Two Longstanding Food Safety Advisory Committees
- Catalyst Food Leaders Announces Virtual Leadership Summit for People in Food
- Food Safety Latam Summit 2025 Set for Mexico City